Harmless treatment method of oil-containing sludge
A treatment method and sludge technology, applied in sludge treatment, water/sludge/sewage treatment, dehydration/drying/concentrated sludge treatment, etc., can solve the problem of high organic content in solid phase, high energy consumption, oily pollution The problem of too much mud, etc., can achieve the effect of strong extraction capacity, reduced energy consumption and low extraction temperature.
- Summary
- Abstract
- Description
- Claims
- Application Information
AI Technical Summary
Problems solved by technology
Method used
Examples
Embodiment 1
[0032] The solvent formula is as follows: distillate oil with a boiling range of 110-125°C is used as the main agent, accounting for 90% (v / v), and distillate oil with a boiling range of 140-150°C is used as an auxiliary agent, accounting for 7% (v / v). / v), distillate oil with a boiling range of 80-100°C, accounting for 3.0% (v / v), forming a composite extractant. Send the oily sludge with a water content of 90% and an oil content of 5% produced by a company into the greenhouse drying room, and place it under sufficient sunlight for 20 days, and use a mud turning machine to turn over the sludge every other day , and keep the drying room well-ventilated. Finally, the water content of the mud cake is 35%, and the oil content is 32%. Then take 1 kg of mud cake and mixed solvent at a mass ratio of 1:8 and mix and extract for 30 minutes. The extraction temperature is 30°C. After the extraction, the solid-liquid mixture is sent to the centrifugal separator, the separated liquid phase...
Embodiment 2
[0036] The solvent formula is as follows: distillate oil with a boiling range of 110-125°C is used as the main agent, accounting for 95% (v / v), and distillate oil with a boiling range of 140-150°C is used as an auxiliary agent, accounting for 4% (v / v), distillate oil with a boiling range of 80-100°C as an auxiliary agent, accounting for 1.0% (v / v), to form a composite extractant. Send the oily sludge with a moisture content of 85% and an oil content of 7% to the greenhouse drying room, and place it under sufficient sunlight for 15 days, turn over the sludge with a mud turning machine every other day, and keep it dry. The chemical room is well ventilated, and the water content of the final mud cake is 34.2%, and the oil content is 45.2%. Then take 1kg of mud cake and mixed solvent, and mix and extract at a mass ratio of 1:10 for 10 minutes at a temperature of 45°C. After the extraction is completed, The solid-liquid mixture is sent to the centrifugal separator, the separated l...
Embodiment 3
[0040] The solvent formula is as follows: distillate oil with a boiling range of 110-125°C is used as the main agent, accounting for 96% (v / v), and distillate oil with a boiling range of 140-150°C is used as an auxiliary agent, accounting for 3% (v / v), distillate oil with a boiling range of 80-100°C as an auxiliary agent, accounting for 1.0% (v / v), to form a composite extractant. That is, the oily sludge with a moisture content of 70% and an oil content of 10% is sent to the greenhouse drying room, and placed under sufficient sunlight for 20 days, and the sludge is turned over with a mud turning machine every 0.5 days, and kept dry. The chemical room is well ventilated, and the water content of the final mud cake is 15%, and the oil content is 47%. Then take 1kg of mud cake and mixed solvent, and mix and extract at a mass ratio of 1:10 for 30 minutes at a temperature of 45°C. After the extraction is completed, The solid-liquid mixture is sent to the centrifugal separator, the...
PUM
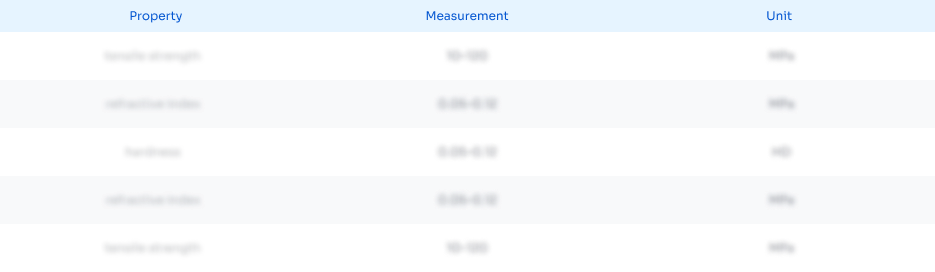
Abstract
Description
Claims
Application Information

- R&D
- Intellectual Property
- Life Sciences
- Materials
- Tech Scout
- Unparalleled Data Quality
- Higher Quality Content
- 60% Fewer Hallucinations
Browse by: Latest US Patents, China's latest patents, Technical Efficacy Thesaurus, Application Domain, Technology Topic, Popular Technical Reports.
© 2025 PatSnap. All rights reserved.Legal|Privacy policy|Modern Slavery Act Transparency Statement|Sitemap|About US| Contact US: help@patsnap.com