Doped modified lithium titanate composite material and preparation method
A kind of technology of lithium titanate and composite materials, applied in the direction of titanium compounds, chemical instruments and methods, inorganic chemistry, etc., can solve the problems of fast capacity decay, poor conductivity, poor electrochemical performance, etc., achieve excellent charge and discharge, improve uniformity The effect of lowering the reaction temperature
- Summary
- Abstract
- Description
- Claims
- Application Information
AI Technical Summary
Problems solved by technology
Method used
Image
Examples
Embodiment 1
[0022] Weigh 6.98g of TiO 2 , 7.58g of lithium formate, 0.0217g of tantalum oxide, 0.0473g of dysprosium oxide and 1.2g of glucose and 1.5g of citric acid were added to the ball mill jar, followed by the addition of 35g of agate balls and 120ml of absolute ethanol, sealed ball mill jar , and ball milled at a speed of 380r / min for 6 hours on a ball mill to obtain a uniformly mixed slurry. Transfer the slurry to a drying dish, put it into an oven and dry it at 80°C to obtain the precursor. Put the precursor powder in a tube furnace, and under the protection of argon, raise the temperature to 500°C at a rate of 120°C / hour and keep it warm for 2 hours to decompose the raw material initially. After the temperature drops to 20-50°C, the calcined powder is obtained. body. Put the calcined powder into a ball mill jar, add 3.0g of soluble starch, then add 25g of agate balls and 50ml of absolute ethanol, and mill on a ball mill at a speed of 400r / min for 12 hours to obtain a uniformly...
Embodiment 2
[0024] Weigh 6.98g of TiO 2 , 4.24g of lithium carbonate, 0.0255g of manganese dioxide, 0.0283g of zirconia and 1.2g of citric acid are added to the ball mill jar, followed by 50g of agate balls and 100ml of absolute ethanol, sealed ball mill jar, on the ball mill Ball milled at a speed of 350r / min for 12 hours to obtain a uniformly mixed slurry. Transfer the slurry to a drying dish, put it into an oven and dry it at 80°C to obtain the precursor. Put the precursor powder in a tube furnace, and under the protection of argon, raise the temperature to 500°C at a rate of 160°C / hour and keep it warm for 5 hours to decompose the raw material initially. After the temperature drops to 20-50°C, the calcined powder is obtained. body. Put the calcined powder into a ball mill jar, add 1.5g of polypropylene alcohol, then add 35g of agate balls and 55ml of absolute ethanol to mix, and mill on a ball mill at a speed of 450r / min for 5 hours to obtain a well-mixed mixture. slurry. Transfer...
Embodiment 3
[0026] Weigh 6.98g of TiO 2 , 7.55g of lithium acetate, 0.0436g of hafnium dioxide, 0.1867g of lanthanum trioxide and 1.5g of glucose are added to the ball mill jar, followed by the addition of 35g of agate balls and 90ml of absolute ethanol, sealed ball mill jar, in the ball mill and ball milled at a speed of 380r / min for 8 hours to obtain a uniformly mixed slurry. Transfer the slurry to a drying dish, put it into an oven and dry it at 80°C to obtain the precursor. Put the precursor powder in a tube furnace, and under the protection of argon, raise the temperature to 500°C at a rate of 180°C / hour and keep it warm for 4 hours to decompose the raw material initially. After the temperature drops to 20-50°C, the calcined powder is obtained body. Put the calcined powder into a ball mill jar, add 3.8g of polyvinyl alcohol, then add 35g of agate balls and 60ml of absolute ethanol, and mill on a ball mill at a speed of 350r / min for 15 hours to obtain a uniformly mixed slurry mater...
PUM
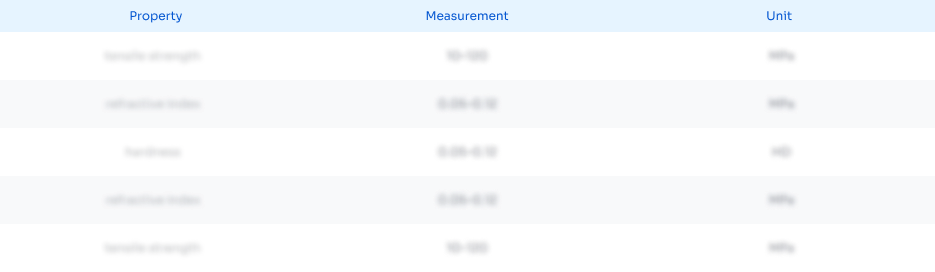
Abstract
Description
Claims
Application Information

- R&D Engineer
- R&D Manager
- IP Professional
- Industry Leading Data Capabilities
- Powerful AI technology
- Patent DNA Extraction
Browse by: Latest US Patents, China's latest patents, Technical Efficacy Thesaurus, Application Domain, Technology Topic, Popular Technical Reports.
© 2024 PatSnap. All rights reserved.Legal|Privacy policy|Modern Slavery Act Transparency Statement|Sitemap|About US| Contact US: help@patsnap.com