Made in a shell
A manufacturing method and shell technology, which is applied in the fields of air conditioners and compressors, can solve problems such as poor alignment, reduced welding strength, and unstable heat, and achieve smooth and bright welding joints, improved welding quality, and stable and controllable heat.
- Summary
- Abstract
- Description
- Claims
- Application Information
AI Technical Summary
Problems solved by technology
Method used
Image
Examples
Embodiment 1
[0029] Such as Figure 4 As shown, the present embodiment is the housing 1 of the compressor accumulator, which consists of a hollow cylinder 12 and three parts, an upper end cover 11 and a lower end cover 13 respectively connected to the two ends of the cylinder 12. to make. Among the parts to be welded, the port diameter of the lower end cover 13 is smaller than the lower port diameter of the barrel 12, the upper port diameter of the barrel 12 is smaller than the port diameter of the upper end cover 11, and the port thickness of each part is the same. Before welding, the two parts to be welded are sleeved and fixedly installed on the fixture. No solder is required between the sleeved surfaces. The welding adopts argon arc welding, and the heating equipment is a single welding gun 4. During welding, control the welding torch 4 to point to the weld 3 between the inner and outer layers of the socket and offset to the outer layer, and the angle between the center axis of the noz...
Embodiment 2
[0031] Such as Figure 5 As shown, the present embodiment is the housing 1 of the compressor accumulator, which consists of a hollow cylinder 12 and three parts, an upper end cover 11 and a lower end cover 13 respectively connected to the two ends of the cylinder 12. to make. Among the parts to be welded, the port diameter of the lower end cover 13 is smaller than the lower port diameter of the barrel 12, the upper port diameter of the barrel 12 is smaller than the port diameter of the upper end cover 11, and the port thickness of each part is the same. Before welding, the two parts to be welded are sleeved and fixedly installed on the fixture. No solder is required between the sleeved surfaces.
[0032] Argon arc welding is used, and the heating equipment is a ring welding torch set at 3 locations corresponding to each weld. There are two ring welding torches. Each ring torch includes three welding torches 4, such as Image 6 As shown, three welding torches 4 are evenly distrib...
Embodiment 3
[0035] In this embodiment, argon arc welding is used. The heating equipment is a ring welding torch set at 3 locations for each welding seam. There are two ring welding torches. Each ring torch includes multiple welding torches 4, which are evenly distributed on the circumference. A torus. According to the diameter of the shell, the number of welding torches and the distribution angle of the circumference should be reasonably distributed, so that the molten metal area of each welding torch overlaps the molten metal area of the adjacent welding torch, then the entire welding circumference can be decomposed into n small molten pools, and The boundaries of each small molten pool overlap. Multiple welding torches start and close the arc at the same time, so as to realize static welding, that is, the three parts to be welded do not rotate, and the welding torch does not rotate, and the entire socket can be sealed and welded in the circumferential direction.
PUM
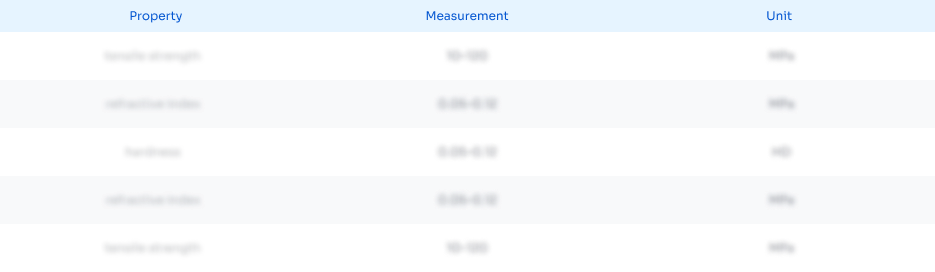
Abstract
Description
Claims
Application Information

- R&D
- Intellectual Property
- Life Sciences
- Materials
- Tech Scout
- Unparalleled Data Quality
- Higher Quality Content
- 60% Fewer Hallucinations
Browse by: Latest US Patents, China's latest patents, Technical Efficacy Thesaurus, Application Domain, Technology Topic, Popular Technical Reports.
© 2025 PatSnap. All rights reserved.Legal|Privacy policy|Modern Slavery Act Transparency Statement|Sitemap|About US| Contact US: help@patsnap.com