Preparation method of SnO2-TiO2 composite nano photocatalyst
A nano-photocatalyst and dilute nitric acid technology, applied in the field of nano-materials and photocatalysis, can solve the problems of low catalyst activity, large amount of smoke, dangerous reaction process, etc., and achieve good catalyst repeatability, good repeatability and short reaction cycle. Effect
- Summary
- Abstract
- Description
- Claims
- Application Information
AI Technical Summary
Problems solved by technology
Method used
Image
Examples
Embodiment 1
[0037] Mix 6ml of tetra-n-butyl titanate, 25ml of absolute ethanol, and 1.5ml of glacial acetic acid, and add 3ml of dilute nitric acid (nitric acid: water = 1:10) drop by drop under continuous stirring to adjust the pH value to 3, and continue stirring for 15 minutes Finally, add 3ml of deionized water, stir for another 10min, then let it stand for 30min, then add 4ml of SnCl with a molar concentration of 1.4mol / L according to the titanium:tin molar ratio of 3:1 4 ·5H 2 O solution, stirred evenly, and aged for 24 hours to slowly polymerize the sol and colloidal particles. The aged sol was transferred to an autoclave and treated at a constant temperature of 180°C for 24 hours, then the product in the autoclave was cooled to room temperature, and the obtained product was centrifuged, dried at 100°C after separation, and then ground into powder. Labeled s-hyth. The powder is calcined in a muffle furnace at 550°C for 4 hours to obtain SnO 2 -TiO 2 solid solution.
Embodiment 2
[0039] Mix 6ml of tetra-n-butyl titanate, 28ml of absolute ethanol, and 2.0ml of glacial acetic acid, and add 3ml of dilute nitric acid (nitric acid: water = 1:10) drop by drop under constant stirring to adjust the pH value to 2, and continue stirring for 15 minutes Finally, add 1ml of deionized water, stir for 10min, then let it stand for 30min, according to the titanium: tin molar ratio of 3:1, add 4ml of SnCl with a molar concentration of 1.4mol / L 4 ·5H 2 O solution, stirred evenly, and aged for 22 hours to slowly polymerize the sol and colloidal particles. The aged sol was transferred to an autoclave and treated at a constant temperature of 175°C for 22 hours, then the product in the autoclave was cooled to room temperature, and the obtained product was centrifuged, dried at 95°C after separation, and then ground into powder. The powder is calcined at 500°C for 6h in a muffle furnace to obtain SnO 2 -TiO 2 solid solution.
Embodiment 3
[0041] Mix 12.5ml of tetra-n-butyl titanate, 52.5ml of absolute ethanol, and 2.5ml of glacial acetic acid evenly, and add 2.5ml of dilute nitric acid (nitric acid: water = 1︰10) dropwise under constant stirring to adjust the pH value to 4. After continuing to stir for 15 minutes, add 7.5ml of distilled water, stir for another 10 minutes, and then let it stand for 30 minutes. According to the titanium: tin molar ratio of 3:1, add 4ml of SnCl with a molar concentration of 1.4mol / L 4 ·5H 2 O solution, stirred evenly, and aged for 26 hours to slowly polymerize the sol and colloidal particles. The aged sol was transferred to an autoclave and treated at a constant temperature of 185°C for 25 hours, then the product in the autoclave was cooled to room temperature, and the obtained product was centrifuged, dried at 110°C after separation, and then ground into powder. The powder is calcined in a muffle furnace at 600°C for 2 hours to obtain SnO 2 -TiO 2 solid solution.
PUM
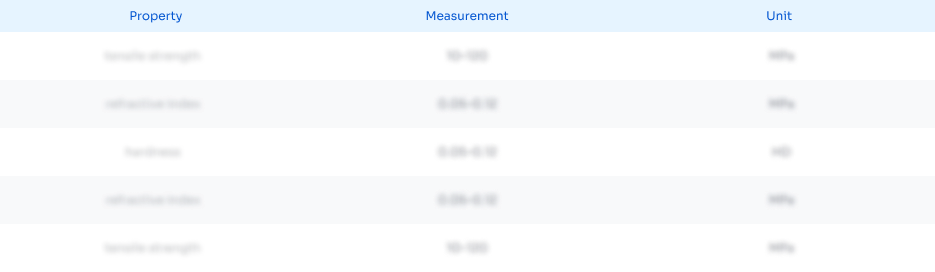
Abstract
Description
Claims
Application Information

- R&D
- Intellectual Property
- Life Sciences
- Materials
- Tech Scout
- Unparalleled Data Quality
- Higher Quality Content
- 60% Fewer Hallucinations
Browse by: Latest US Patents, China's latest patents, Technical Efficacy Thesaurus, Application Domain, Technology Topic, Popular Technical Reports.
© 2025 PatSnap. All rights reserved.Legal|Privacy policy|Modern Slavery Act Transparency Statement|Sitemap|About US| Contact US: help@patsnap.com