Semisteel steelmaking carbon content control method and semisteel steelmaking method
A control method and carbon content technology, which are applied in the field of semi-steel steelmaking, can solve the problems of physical temperature difference in semi-steel steelmaking, and achieve the effects of controlling the consumption of steel materials, avoiding low utilization rate, and increasing the temperature of molten steel
- Summary
- Abstract
- Description
- Claims
- Application Information
AI Technical Summary
Problems solved by technology
Method used
Examples
example 1
[0021] In this example, the semi-steel is molten steel after vanadium-containing molten iron has been blown in a vanadium-extracting converter, and contains 3.52% C and 0.01% Si by weight percentage.
[0022] In the process of removing semi-steel from the ladle, 1.5kg / (t semi-steel) of ferrosilicon and 5kg / (t semi-steel) of silicon carbide are added to the ladle; then the semi-steel is blended into the steelmaking furnace, Oxygen blowing smelting with oxygen lance and adding 35kg / (t semi-steel) lime, 15kg / (t semi-steel) high magnesium lime, 1kg / (t semi-steel) composite slagging agent according to blowing, the initial slag formation time is 2.2min , After the temperature of the molten steel reaches 1670°C, the oxygen lance is raised and the blowing is stopped. The carbon content of the obtained molten steel is 0.08%, and the steel material consumption per ton of steel is 1050kg.
example 2
[0024] In this example, the semi-steel is the molten steel after the vanadium-containing molten iron is blown by the vanadium-extracting converter, and it contains 3.47% C and 0.01% Si by weight percentage.
[0025]In the process of discharging semi-steel into the ladle, 6kg / (t semi-steel) of ferrosilicon and 1kg / (t semi-steel) of silicon carbide are added to the ladle; then the semi-steel is mixed into the steelmaking furnace, and the Oxygen blowing smelting with oxygen lance and adding 36kg / (t semi-steel) lime and 10kg / (t semi-steel) high-magnesium lime according to blowing. The initial slag formation time is 2.6min. After the molten steel temperature reaches 1680°C, the oxygen lance is taken out Stop blowing. The carbon content of the obtained molten steel is 0.11%, and the steel material consumption per ton of steel is 1051kg.
example 3
[0027] In this example, the semi-steel is molten steel after vanadium-containing molten iron has been blown in a vanadium-extracting converter, and contains 3.55% C and 0.02% Si by weight percentage.
[0028] After blending the semi-steel into the steelmaking converter, add 1.5kg / (t semi-steel) of ferrosilicon and 5kg / (t semi-steel) of silicon carbide into the steelmaking converter; / (t semi-steel) lime, 13kg / (t semi-steel) high-magnesium lime, the initial slag formation time is 3.1min, after the molten steel temperature reaches 1690°C, take out the oxygen lance and stop blowing. The carbon content of the obtained molten steel is 0.06%, and the steel material consumption per ton of steel is 1049kg.
PUM
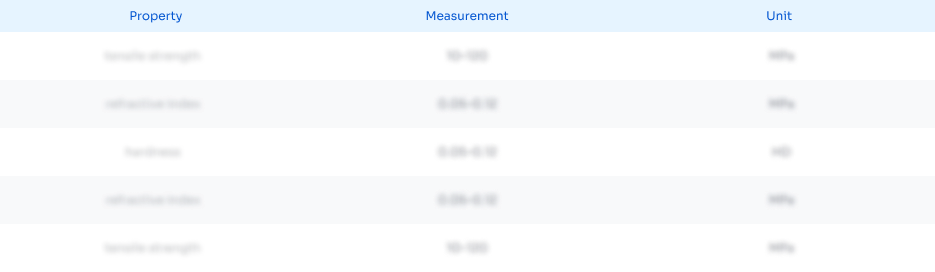
Abstract
Description
Claims
Application Information

- R&D
- Intellectual Property
- Life Sciences
- Materials
- Tech Scout
- Unparalleled Data Quality
- Higher Quality Content
- 60% Fewer Hallucinations
Browse by: Latest US Patents, China's latest patents, Technical Efficacy Thesaurus, Application Domain, Technology Topic, Popular Technical Reports.
© 2025 PatSnap. All rights reserved.Legal|Privacy policy|Modern Slavery Act Transparency Statement|Sitemap|About US| Contact US: help@patsnap.com