Method for preparing full acetylation cellulose
A technology of full acetylation and cellulose, applied in the field of preparation of full acetylated cellulose, can solve the problems of lack of cellulose transesterification catalyst, difficulty in realizing cellulose full acetylation, aggravating cellulose degradation, etc., and achieve product purification Simple and easy to operate, improve the efficiency of transesterification reaction, and easy to operate
- Summary
- Abstract
- Description
- Claims
- Application Information
AI Technical Summary
Problems solved by technology
Method used
Image
Examples
Embodiment 1
[0025] The cellulose of this embodiment is fully acetylated under efficient and mild conditions, and its specific preparation process is as follows:
[0026] Step 1. Disperse 0.1g of linter cellulose into dimethyl sulfoxide (DMSO) to obtain a cellulose suspension, the mass volume ratio of cellulose to DMSO is 1g:40mL;
[0027] Step 2. join acylating reagent IPA and catalyzer DBU in the cotton linter cellulose suspension obtained in step 1, the mol ratio of the anhydroglucose unit of IPA and cotton linter cellulose is 4:1, DBU and acyl The volume ratio of the reagent IPA is 1:5, and the esterification reaction is carried out at 60°C under air-isolated conditions. The reaction time is 15 hours, and the reaction process is kept uniformly stirred;
[0028] Step 3. After the esterification reaction is completed, pour the reaction solution into 100mL of a mixture of ethanol and water (volume ratio: 1:2) to terminate the reaction, stir well and filter, and wash the precipitate with e...
Embodiment 2
[0031] The cellulose of this embodiment is fully acetylated under efficient and mild conditions, and its specific preparation process is as follows:
[0032] Step 1. Disperse 0.1g of eucalyptus cellulose into dimethyl sulfoxide (DMSO) to obtain a cellulose suspension, and the mass volume ratio of cellulose to DMSO is 1:20 (g / mL);
[0033] Step 2. join acylating reagent IPA and catalyst DBU in the eucalyptus wood cellulose suspension that obtains in step 1, the mol ratio of IPA and cellulose anhydroglucose unit is 6:1, the volume of DBU and acylating reagent IPA The ratio is 1:10, and the esterification reaction is carried out at 110°C under air-isolated conditions, the reaction time is 6h, and the reaction process is kept uniformly stirred;
[0034] Step 3. After the esterification reaction is completed, pour the reaction solution into 100mL of a mixture of ethanol and water (volume ratio: 1:2) to terminate the reaction, stir well and filter, and wash the precipitate with etha...
Embodiment 3
[0037] The cellulose of this embodiment is fully acetylated under efficient and mild conditions, and its specific preparation process is as follows:
[0038] Step 1. Disperse 0.1g of bagasse cellulose into dimethyl sulfoxide (DMSO) to obtain a cellulose suspension, and the mass volume ratio of cellulose to DMSO is 1:10 (g / mL);
[0039] Step 2. join acylating reagent IPA and catalyst DBU in the eucalyptus wood cellulose suspension that obtains in step 1, the mol ratio of IPA and cellulose anhydroglucose unit is 10:1, the volume of DBU and acylating reagent IPA The ratio is 1:20, and the esterification reaction is carried out at 130°C under air-isolated conditions, the reaction time is 2h, and the reaction process is kept uniformly stirred;
[0040] Step 3. After the esterification reaction is completed, pour the reaction solution into 100mL of a mixture of ethanol and water (volume ratio: 1:2) to terminate the reaction, stir thoroughly and filter, and wash the precipitate with ...
PUM
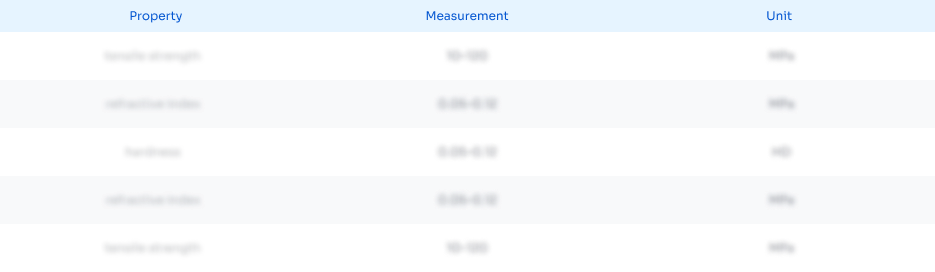
Abstract
Description
Claims
Application Information

- Generate Ideas
- Intellectual Property
- Life Sciences
- Materials
- Tech Scout
- Unparalleled Data Quality
- Higher Quality Content
- 60% Fewer Hallucinations
Browse by: Latest US Patents, China's latest patents, Technical Efficacy Thesaurus, Application Domain, Technology Topic, Popular Technical Reports.
© 2025 PatSnap. All rights reserved.Legal|Privacy policy|Modern Slavery Act Transparency Statement|Sitemap|About US| Contact US: help@patsnap.com