Preparation method of high-purity copper oxide powder material
A technology of copper oxide powder and bulk material, applied in copper oxide/copper hydroxide and other directions, can solve the problems of complex process flow, high preparation cost, large amount of chemical agent, etc., and achieve the effect of shortening the process flow
- Summary
- Abstract
- Description
- Claims
- Application Information
AI Technical Summary
Problems solved by technology
Method used
Image
Examples
Embodiment 1
[0020] 1) Remove the varnish from the Ф2mm red copper wire, and after cleaning, cut it into small pieces with a length of 5-10mm and a weight of 200Kg.
[0021] 2) Put the prepared small pieces into a rotary furnace inlaid with a pure copper liner for heating, and the thickness of the liner is 12mm; put 600Kg of red copper grinding balls, of which 120Kg for a diameter of 60mm, 180Kg for a diameter of 45mm, and 180Kg for a diameter of 25mm The weight is 300Kg; the load in the furnace is between 20% and 35%; the oxidation temperature is 500°C; the rotating speed of the rotary furnace is 20r / min; the oxidation time is 240min; 15m 3 / h.
[0022] 3) Use a vibrating screen to separate the grinding balls from the copper oxide powder, and obtain the copper oxide powder material after cooling.
[0023] The product obtained in this embodiment is characterized by X-ray diffraction spectrum, as figure 1 shown. It can be seen from the figure that there is no impurity in the product and...
Embodiment 2
[0025] 1) Clean the red copper rod of Ф10mm with water and cut it into small pieces with a length of 5-10mm and a weight of 500Kg with a shear.
[0026] 2) Put the prepared small pieces into a rotary furnace inlaid with a high-temperature-resistant stainless steel (310s) lining plate for heating, and the thickness of the lining plate is 10mm; put 500Kg of copper balls, of which the weight of 60mm in diameter is 100Kg, and the weight of 45mm in diameter is 150Kg. The weight is 250Kg with a diameter of 25mm; the load in the furnace is between 20% and 35%; the oxidation temperature is 900°C; the rotation speed of the rotary furnace is 5r / min; the oxidation time is 600min; Oxygen flow rate is 10m 3 / h.
[0027] 3) Use a vibrating screen to separate the grinding balls from the copper oxide powder, and obtain the copper oxide powder material after cooling.
[0028] The product obtained in this embodiment is characterized by X-ray diffraction spectrum, as figure 2 shown. It can ...
PUM
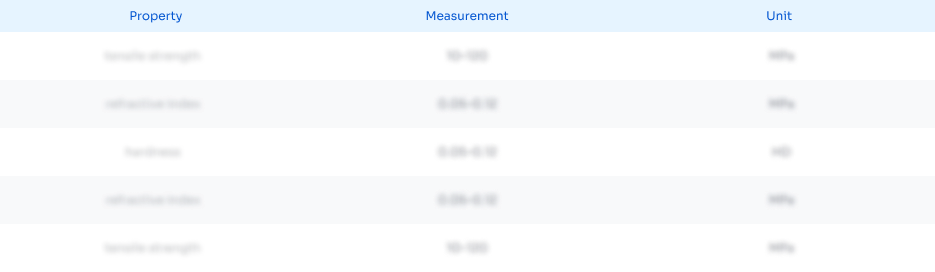
Abstract
Description
Claims
Application Information

- R&D
- Intellectual Property
- Life Sciences
- Materials
- Tech Scout
- Unparalleled Data Quality
- Higher Quality Content
- 60% Fewer Hallucinations
Browse by: Latest US Patents, China's latest patents, Technical Efficacy Thesaurus, Application Domain, Technology Topic, Popular Technical Reports.
© 2025 PatSnap. All rights reserved.Legal|Privacy policy|Modern Slavery Act Transparency Statement|Sitemap|About US| Contact US: help@patsnap.com