Three-phase compensation dynamic reactive power compensation device
A three-phase co-compensation and power compensation technology, applied in reactive power adjustment/elimination/compensation, reactive power compensation and other directions, can solve problems such as failure to suppress and filter, lack of overload capability, and sensitivity to system parameters. Achieve the effects of light weight, improved system stability, and high magnetic induction performance
- Summary
- Abstract
- Description
- Claims
- Application Information
AI Technical Summary
Problems solved by technology
Method used
Image
Examples
Embodiment 1
[0064] Copper (Cu) 5, niobium (Nb) 1, chromium (Cr) 0.5, silicon (Si) 2, boron (B) 10, iron (Fe) 81.5. Nanomaterials are pressed by powder metallurgy, and the magnetic permeability ui can reach more than 150,000.
Embodiment 2
[0066] Copper (Cu) 6, niobium (Nb) 0.5, chromium (Cr) 1, silicon (Si) 3, boron (B) 12, iron (Fe) 77.5, nano-materials, pressed by powder metallurgy, magnetic permeability ui can be Reach more than 120,000.
Embodiment 3
[0068] Copper (Cu) 7, niobium (Nb) 1.5, chromium (Cr) 1, silicon (Si) 5, boron (B) 15, iron (Fe) 70.5, nano material, pressed by powder metallurgy, magnetic permeability ui can be Reach more than 200,000.
[0069] The three-phase co-compensation dynamic reactive power compensation device can be used in series to meet the needs of different powers. Such as figure 2 .
[0070] The following is figure 1 and figure 2 The dynamic reactive power compensation device needs to be equipped with auxiliary equipment and parameter data charts (see Figure 5 ).
PUM
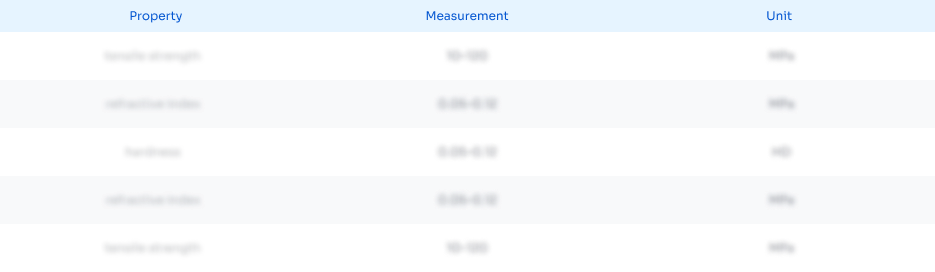
Abstract
Description
Claims
Application Information

- Generate Ideas
- Intellectual Property
- Life Sciences
- Materials
- Tech Scout
- Unparalleled Data Quality
- Higher Quality Content
- 60% Fewer Hallucinations
Browse by: Latest US Patents, China's latest patents, Technical Efficacy Thesaurus, Application Domain, Technology Topic, Popular Technical Reports.
© 2025 PatSnap. All rights reserved.Legal|Privacy policy|Modern Slavery Act Transparency Statement|Sitemap|About US| Contact US: help@patsnap.com