Construction Method of Adaptive Inverse Controller for Axial Hybrid Magnetic Bearings of Bearingless Motors
A bearingless motor and axial hybrid technology, applied in the direction of adaptive control, bearing, shaft and bearing, etc., can solve the problems of hybrid magnetic bearing system rapidity and overshoot, integral saturation, hybrid magnetic bearing system oscillation, etc. , to achieve good following characteristics, easy to achieve adjustment, eliminate interference and noise
- Summary
- Abstract
- Description
- Claims
- Application Information
AI Technical Summary
Problems solved by technology
Method used
Image
Examples
Embodiment Construction
[0022] The concrete implementation of the present invention divides following 6 steps:
[0023] 1. If figure 1 As shown, the switching power amplifier 1, the axial hybrid magnetic bearing 2 of the bearingless motor, the load 3 and the eddy current displacement sensor 4 are taken as a whole to form a compound controlled object 5 . The load 3 is connected to the axial hybrid magnetic bearing 2 of the bearingless motor, the switching power amplifier 1 is connected in series before the axial hybrid magnetic bearing 2 of the bearingless motor, and the eddy current displacement sensor 4 is inside the axial hybrid magnetic bearing 2 of the bearingless motor for Detect the axial displacement of the axial hybrid magnetic bearing 2 of the bearingless motor. A given axial control current After passing through the switching power amplifier 1, two currents i are obtained 0 + i z i 0 -i z , where i 0 is the bias current, i z control current, the two currents i 0 + i z i 0 -i z ...
PUM
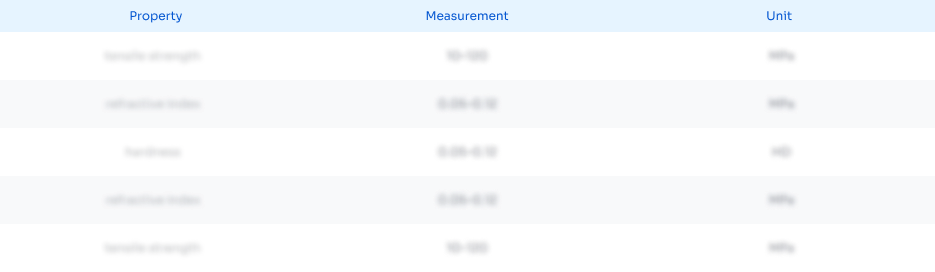
Abstract
Description
Claims
Application Information

- R&D
- Intellectual Property
- Life Sciences
- Materials
- Tech Scout
- Unparalleled Data Quality
- Higher Quality Content
- 60% Fewer Hallucinations
Browse by: Latest US Patents, China's latest patents, Technical Efficacy Thesaurus, Application Domain, Technology Topic, Popular Technical Reports.
© 2025 PatSnap. All rights reserved.Legal|Privacy policy|Modern Slavery Act Transparency Statement|Sitemap|About US| Contact US: help@patsnap.com