Preparation method and application for reaction-type halogen-containing flame-retardant polyether polyol
A flame retardant polyether and polyol technology is applied in the preparation of polyether polyol and the preparation of reactive halogen-containing flame retardant polyether polyol, which can solve the problems of high price, low functionality, high viscosity, etc. The effect of moderate viscosity, good compatibility and excellent mechanical properties
- Summary
- Abstract
- Description
- Claims
- Application Information
AI Technical Summary
Problems solved by technology
Method used
Examples
Embodiment 1
[0027] 1. Weigh 261g of dibromoneopentyl glycol and add it to a 1L four-necked flask with mechanical stirring, thermometer, dropping funnel and condenser tube, and simultaneously weigh 460g of epichlorohydrin and add it to the dropping funnel (dibromoneopentyl glycol) The molar ratio of pentylene glycol to epichlorohydrin is 1:4.97), heat the solid material to 120°C until it is completely melted, add 1.1g of oleum, and start adding epichlorohydrin dropwise at 120°C, drop After completion, the insulation was continued for 4 hours to obtain difunctional polyepichlorohydrin with a reaction yield of 99%.
[0028] 2. Cool the product obtained in the first step reaction to 40°C, add 160g of 50wt% sodium hydroxide aqueous solution (the molar ratio of sodium hydroxide to polyepichlorohydrin is 2:1), stir at 50°C for 3 hours, and let it stand Set liquid separation, after separating the dark brown liquid in the lower layer, carry out vacuum distillation at 90 ℃ to remove a small amount ...
Embodiment 2
[0033] 1. Weigh 505g of tetrabromodipentaerythritol and add it to a 1L four-neck flask with a mechanical stirrer, a thermometer, a dropping funnel and a condenser tube, and simultaneously weigh 388g of epichlorohydrin and add it to the dropping funnel (tetrabromodipentaerythritol and The molar ratio of epichlorohydrin is 1:4.2), heat the solid material to 110°C until it is completely melted, add 5g of fuming sulfuric acid, keep 110°C and start adding epichlorohydrin dropwise, and continue to keep warm for 5 Hour, obtain the polyepichlorohydrin of bifunctionality, reaction yield 99%.
[0034] 2. Cool the product obtained in the first step to 40°C, add 80g of 50wt% sodium hydroxide ethanol solution (the molar ratio of sodium hydroxide to polyepichlorohydrin is 1:1), and stir at 60°C for 4 hours Stand for liquid separation, separate the dark brown liquid in the lower layer, carry out vacuum distillation at 90°C to remove a small amount of water, and finally filter to remove resid...
Embodiment 3
[0039]1. Weigh 543g of tetrabromobisphenol A and 162g of epichlorohydrin, and add them to a 2L four-neck flask with mechanical stirring, thermometer, dropping funnel and condenser tube, and weigh 578g of epichlorohydrin to add the dripping solution Funnel (the molar ratio of tetrabromobisphenol A to epichlorohydrin is 1:8), heat the solid material to 120°C until it is completely melted, add 4.3g perchloric acid, keep 120°C and start dripping epoxy chlorine Propane, continue to keep warm for 8 hours after the dropwise addition is completed, to obtain difunctional polyepichlorohydrin, and the reaction yield is 99%.
[0040] 2. Cool the product obtained in the first step reaction to 50°C, add 336g of 50wt% potassium hydroxide aqueous solution (the molar ratio of potassium hydroxide to polyepichlorohydrin is 3:1), stir at 50°C for 3 hours and then statically Set liquid separation, after separating the dark brown liquid in the lower layer, carry out vacuum distillation at 90°C to r...
PUM
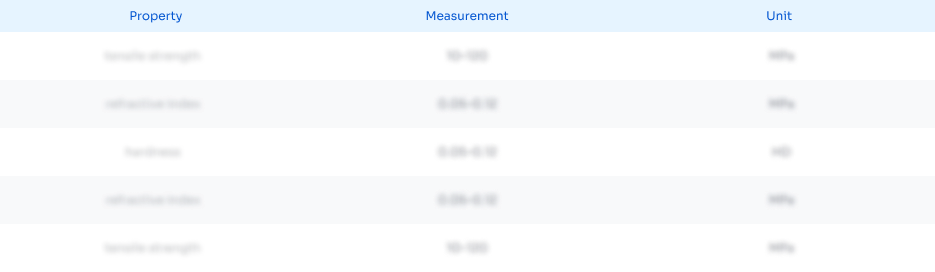
Abstract
Description
Claims
Application Information

- R&D
- Intellectual Property
- Life Sciences
- Materials
- Tech Scout
- Unparalleled Data Quality
- Higher Quality Content
- 60% Fewer Hallucinations
Browse by: Latest US Patents, China's latest patents, Technical Efficacy Thesaurus, Application Domain, Technology Topic, Popular Technical Reports.
© 2025 PatSnap. All rights reserved.Legal|Privacy policy|Modern Slavery Act Transparency Statement|Sitemap|About US| Contact US: help@patsnap.com