Testing device for mechanical property of material
A testing device and a technology of material mechanics, applied in the direction of measuring devices, analytical materials, scientific instruments, etc., can solve problems such as clamping difficulties, single test methods, and inability to conduct in-depth research on the combination of composite loads and material denaturation damage processes. To achieve the effect of compact structure and high degree of compounding
- Summary
- Abstract
- Description
- Claims
- Application Information
AI Technical Summary
Problems solved by technology
Method used
Image
Examples
Embodiment Construction
[0029] Embodiments of the present invention will be described in detail below in conjunction with the accompanying drawings.
[0030] A device for testing mechanical properties of materials in the present invention includes a working platform 1 provided with supporting feet 10 for supporting, on the working platform 1 there are slide rails 2 perpendicular to each other along the X-axis and Y-axis directions, and along the X-axis The slide rail 2 arranged in the direction and the slide rail 2 arranged along the Y-axis direction are provided with a first stretching seat 21 and a second stretching seat 22 for stretching the specimen, and on the back of the working platform 1 there is a A stretching seat 21 and a second stretching seat 22 move toward or back to the tensile load driving device 3, and the first stretching seat 21 and the second stretching seat 22 arranged along the X-axis and Y-axis directions are connected There is a clamping device 5 for clamping the test piece. B...
PUM
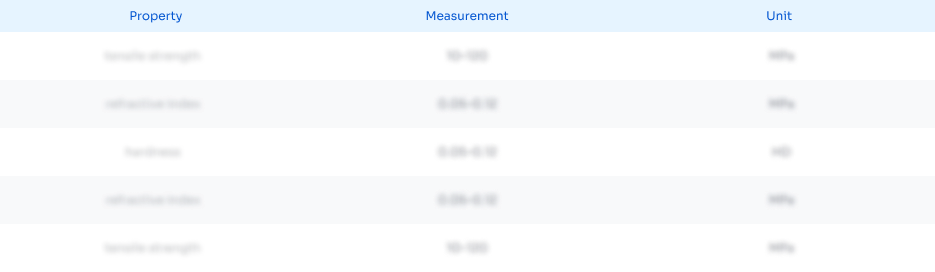
Abstract
Description
Claims
Application Information

- Generate Ideas
- Intellectual Property
- Life Sciences
- Materials
- Tech Scout
- Unparalleled Data Quality
- Higher Quality Content
- 60% Fewer Hallucinations
Browse by: Latest US Patents, China's latest patents, Technical Efficacy Thesaurus, Application Domain, Technology Topic, Popular Technical Reports.
© 2025 PatSnap. All rights reserved.Legal|Privacy policy|Modern Slavery Act Transparency Statement|Sitemap|About US| Contact US: help@patsnap.com