Method for reducing organic chloride content of hydrocarbon fuel oil
A technology of organochlorine and fuel oil, applied in the field of chemical industry, can solve problems such as environmental pollution, corrosion of equipment, catalyst poisoning, etc., and achieve the effects of reducing investment costs, easy enlargement, and simple operation process
- Summary
- Abstract
- Description
- Claims
- Application Information
AI Technical Summary
Problems solved by technology
Method used
Examples
Embodiment 1
[0029] It was determined that the organic chlorine content of the raw hydrocarbon fuel was 6429ppm. By mass ratio m 烃类燃油 :m 脱氯剂 :m 溶剂 :m 助剂 =100:5:30:1 ratio, weigh 50g of hydrocarbon fuel, 2.5g of dechlorination agent, 15g of solvent and 0.5g of auxiliary agent (dechlorination agent is sodium hydroxide, anhydrous sodium acetate, urea, sodium silicate , zinc powder, sodium methoxide, the solvent is any one of DMF and distilled water, and the auxiliary agent is CTAB), and then add it to the stirring reaction kettle with a condensing reflux device at the same time. Heating and stirring the reaction, and reacting at the set temperature for a certain period of time, then carry out atmospheric distillation to separate and purify, and the obtained fraction is the product after dechlorination, and its organic chlorine content is measured. The specific reaction parameter settings and results are shown in Table 1:
[0030] Table 1
[0031] Dechlorination agent solvent...
Embodiment 2
[0035] It was determined that the organic chlorine content of the raw hydrocarbon fuel was 6429ppm. By mass ratio m 烃类燃油 :m 脱氯剂 :m 溶剂 :m 助剂 =100:4:40:0 ratio, weigh 50g of hydrocarbon fuel, 2.0g of dechlorination agent and 20g of solvent (dechlorination agent is sodium methoxide, solvent is any one of DMSO, DMF, THF), and then, At the same time, it is added to the stirred reactor with a condensing reflux device. Heat and stir for reaction, and react at 110°C for 6 hours, then carry out atmospheric distillation to separate and purify, the obtained fraction is the product after dechlorination, and its organic chlorine content is measured. The results are shown in Table 2.
[0036] Table 2
[0037] Dechlorination agent solvent Product chlorine content (ppm) Sodium methoxide DMF 43 Sodium methoxide DMSO 24 Sodium methoxide THF 2119
[0038] It can be seen from Table 2 that when sodium methoxide is used as the dechlorination agent, a...
Embodiment 3
[0041] It was determined that the organic chlorine content of the raw hydrocarbon fuel was 6429ppm. By mass ratio m 烃类燃油 :m 脱氯剂 :m 溶剂 :m 助剂=100:2:20:1 ratio, weigh 50g of hydrocarbon fuel, 1.0g of sodium methoxide, 10g of DMSO and 0.5g of CTAB, and then add them into a stirred reactor with a condensing reflux device at the same time. Heated and stirred for reaction, and reacted at 110°C for 6 hours, then carried out atmospheric distillation for separation and purification, and the obtained fraction was the product after dechlorination, and its organic chlorine content was determined to be 3992ppm.
[0042]
PUM
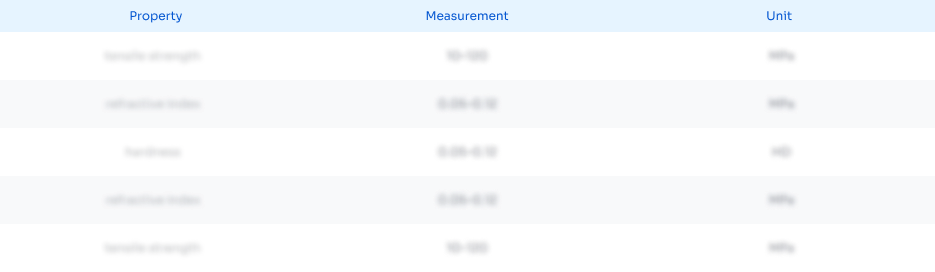
Abstract
Description
Claims
Application Information

- Generate Ideas
- Intellectual Property
- Life Sciences
- Materials
- Tech Scout
- Unparalleled Data Quality
- Higher Quality Content
- 60% Fewer Hallucinations
Browse by: Latest US Patents, China's latest patents, Technical Efficacy Thesaurus, Application Domain, Technology Topic, Popular Technical Reports.
© 2025 PatSnap. All rights reserved.Legal|Privacy policy|Modern Slavery Act Transparency Statement|Sitemap|About US| Contact US: help@patsnap.com