Low-density high-strength ceramsite proppant and preparation method thereof
A high-strength, low-density technology, applied in chemical instruments and methods, earth-moving drilling, clay products, etc., can solve the problems of non-renewable energy reduction, environmental pollution, rising prices, etc., to change the market structure, low acid solubility, Low turbidity effect
- Summary
- Abstract
- Description
- Claims
- Application Information
AI Technical Summary
Problems solved by technology
Method used
Examples
Embodiment 1
[0024] The ceramsite proppant of this embodiment is composed of the following parts by mass of raw materials: bauxite tailings (Al 2 O 3 : 25%, SiO 2 : 65%, Fe 2 O 3 :5%) 33 parts, burnt gems (Al 2 O 3 : 55%, SiO 2 :40%) 39 parts, quartz sand (Al 2 O 3 : 3%, SiO 2 : 95%, Fe 2 O 3 :1%) 7 parts, iron red powder (Fe 2 O 3 : 97%) 7 parts and 2 parts of alumina powder.
[0025] The preparation steps are as follows:
[0026] Various raw materials are crushed to a particle diameter of less than 0.056mm. After the raw materials are fully mixed according to the proportions, they are ground for 1.5 hours with a ball mill. The slurry passes through a 600-mesh screen with a pass rate of more than 99%. The slurry is pumped to spray drying The tower is dried, and the dried mixed powder is placed in a strong granulator to form a particle size of 1mm and then dried. After 18-30 meshes, the semi-finished product is transported to the rotary kiln for calcination. The calcination temperature is 1100°C...
Embodiment 2
[0028] The ceramsite proppant of this embodiment is composed of the following parts by mass of raw materials: bauxite tailings (Al 2 O 3 : 35%, SiO 2 : 55%, Fe 2 O 3 :7%) 45 copies, burnt gems (Al 2 O 3 : 40%, SiO 2 : 50%, Fe 2 O 3 : 1%) 43 parts, quartz sand (Al 2 O 3 : 2%, SiO 2 : 95%, Fe 2 O 3 :1%) 12 parts, iron red powder (Fe 2 O 3 : 98%) 5 parts and 5 parts of alumina powder.
[0029] The various raw materials are crushed to a particle diameter of less than 0.056mm. After the raw materials are fully mixed according to the proportion, they are ground for 1.8 hours with a ball mill. The slurry passes through a 700 mesh screen with a pass rate of more than 99%. Pump the slurry to spray The drying tower is dried, and the dried mixed powder is placed in a strong granulator to form a particle size of 1mm. After 18-30 mesh, it is a semi-finished product and is transported to a rotary kiln for calcination. The calcination temperature is 1300℃ and the calcination time is 3 hours , Th...
Embodiment 3
[0031] The ceramsite proppant of this embodiment is composed of the following parts by mass of raw materials: bauxite tailings (Al 2 O 3 : 30%, SiO 2 : 60%, Fe 2 O 3 :6%) 53 parts, burnt gems (Al 2 O 3 :50%, SiO 2 :48%) 27 parts, quartz sand (Al 2 O 3 : 1%, SiO 2 : 96%, Fe 2 O 3 : 1%) 6 parts, iron red powder (Al 2 O 3 : 1%, Fe 2 O 3 : 96%) 2 parts and 10 parts of alumina powder.
[0032] Various raw materials are crushed to a particle diameter of less than 0.056mm. After the raw materials are fully mixed according to the proportion, they are ground for 2 hours with a ball mill. The slurry passes through an 800-mesh screen with a pass rate of more than 99%. Pump the slurry to spray The drying tower is dried, and the dried mixed powder is placed in a strong granulator to form a particle size of 1mm. After 18-30 mesh, it is a semi-finished product and is transported to a rotary kiln for calcination. The calcination temperature is 1500°C and the calcination time is 5 hours. , Then co...
PUM
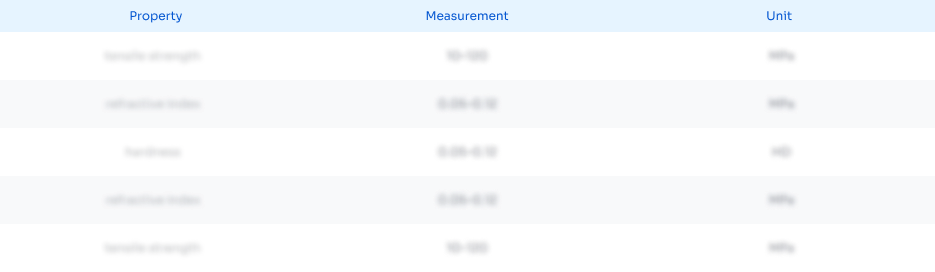
Abstract
Description
Claims
Application Information

- R&D
- Intellectual Property
- Life Sciences
- Materials
- Tech Scout
- Unparalleled Data Quality
- Higher Quality Content
- 60% Fewer Hallucinations
Browse by: Latest US Patents, China's latest patents, Technical Efficacy Thesaurus, Application Domain, Technology Topic, Popular Technical Reports.
© 2025 PatSnap. All rights reserved.Legal|Privacy policy|Modern Slavery Act Transparency Statement|Sitemap|About US| Contact US: help@patsnap.com