Preparation method of glycidyl terminated allyl alcohol polyoxyethylene ether
A technology of terminal allyl alcohol polyoxyethylene ether and allyl alcohol polyoxyethylene ether, which is applied in the field of preparation of glycidyl-terminated allyl alcohol polyoxyethylene ether, and can solve the problem that the color and luster of the product are unsatisfactory and the product Color influence, strong alkalinity of sodium hydride, etc., to achieve the effect of high double bond protection rate, prevention of color darkening, and less side reactions
- Summary
- Abstract
- Description
- Claims
- Application Information
AI Technical Summary
Problems solved by technology
Method used
Image
Examples
Embodiment 1
[0033] In this example, 300g H 2 O, 160g NaOH and 48g CaCl 2 Put it into a 2L pressure reactor, raise the temperature to 110°C, stir for 0.5h, and then vacuumize and dehydrate to dryness. Fill the kettle with nitrogen to normal pressure, lower the temperature to 25°C, continue to add 5g of P.T.C (tetra-n-butylammonium bromide) and 984g of APEG (average molecular weight: 492g / moL), and replace the nitrogen with vacuum. Then, 555g of ECH was passed into the dripping storage tank, and at the same time, the temperature was lowered to below 25°C, and the nitrogen was replaced by vacuuming. The temperature of the pressure reactor was raised to 35°C, and ECH was slowly added dropwise. After the dropwise addition, the reaction was continued for 5 hours and the material was discharged. Remove salt by filtration, neutralize with phosphoric acid, recover ECH (about 342.9g) by vacuuming, and add acid clay to refine. The resulting product has a color of 40, a capping rate of 93.2%, and ...
Embodiment 2
[0035] In this example, 300g H 2 O, 120g NaOH and 24g CaCl 2 Put it into a 2L pressure reactor, raise the temperature to 90°C, stir for 0.5h, and then vacuumize and dehydrate to dryness. Fill the kettle with nitrogen to normal pressure, lower the temperature to 25°C, continue to add 3g of P.T.C (trioctylmethylammonium chloride) and 984g of APEG (average molecular weight: 492g / moL), and replace the nitrogen with vacuum. Then, 740g of ECH was passed into the drip storage tank, and at the same time, the temperature was lowered to below 25°C, and the nitrogen was replaced by vacuuming. The temperature of the pressure reactor was raised to 45°C, ECH was slowly added dropwise, and after the end of the dropwise addition, the reaction was continued for 2 hours and the material was discharged. Filter to remove salt, phosphoric acid neutralize, vacuumize to recover ECH (about 530g), add magnesium silicate to refine. The resulting product has a color of 40, a capping rate of 92.8%, an...
Embodiment 3
[0037] In this example, 210g H 2 O, 140g NaOH and 70g CaCl 2Put it into a 2L pressure reactor, raise the temperature to 120°C, stir for 0.5h, and then vacuumize and dehydrate to dryness. Fill the kettle with nitrogen to normal pressure, lower the temperature to 25°C, continue to add 4g of P.T.C (tetraethylammonium chloride) and 984g of APEG (average molecular weight: 492g / moL), and replace the nitrogen with vacuum. Then, 279g of ECH was passed into the dripping storage tank, and at the same time, the temperature was lowered to below 25°C, and the nitrogen was replaced by vacuuming. The temperature of the pressure reactor was raised to 32°C, ECH was slowly added dropwise, and after the end of the dropwise addition, the reaction was continued for 7h and the material was discharged. Remove salt by filtration, neutralize phosphoric acid, recover ECH (about 530g) by vacuuming, and add activated carbon for refining. The resulting product has a color of 40, a capping rate of 92.4%...
PUM
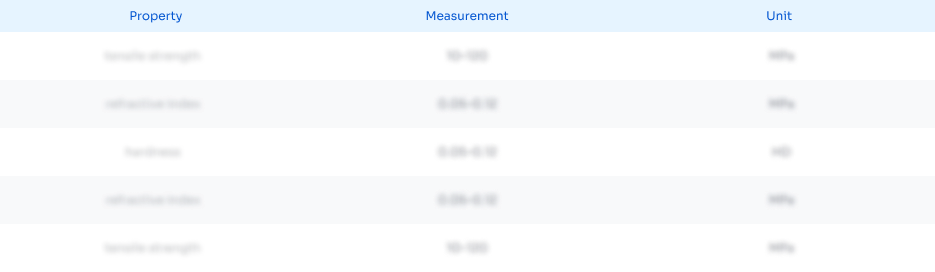
Abstract
Description
Claims
Application Information

- R&D
- Intellectual Property
- Life Sciences
- Materials
- Tech Scout
- Unparalleled Data Quality
- Higher Quality Content
- 60% Fewer Hallucinations
Browse by: Latest US Patents, China's latest patents, Technical Efficacy Thesaurus, Application Domain, Technology Topic, Popular Technical Reports.
© 2025 PatSnap. All rights reserved.Legal|Privacy policy|Modern Slavery Act Transparency Statement|Sitemap|About US| Contact US: help@patsnap.com