Polyether ester polyurethane elastomer and preparation method thereof
A polyurethane elastomer and polyurethane prepolymer technology, applied in the field of polyether ester polyurethane elastomer, can solve the problems of poor hydrolysis resistance and poor mechanical properties, and achieve improved hydrolysis resistance, excellent comprehensive performance, and good application prospects Effect
- Summary
- Abstract
- Description
- Claims
- Application Information
AI Technical Summary
Problems solved by technology
Method used
Image
Examples
preparation example Construction
[0029] Preparation of polyether ester polyol: polyether ester polyol is based on polyester polyol as starter, in bimetallic catalyst DMC (such as Zn 3 [Co(CN) 6 ] 2 ) in the presence of propylene oxide ring-opening polymerization, Mn = 2000, its preparation method see patent CN101024684A.
[0030] (1) In a pressure-resistant reactor with a volume of 225 ml, add polyester polyols made of dibasic acids and diols, double metal cyanide complex catalyst DMC, heat to 105±3°C, and vacuum After removing water and volatile components, mix for 5 minutes in an ultrasonic mixer with a frequency of 40KHz and a power of 500 watts;
[0031] (2) Add a part of propylene oxide into the pressure-resistant reaction kettle in (1) above under the conditions of 110±3℃, nitrogen protection and stirring, and after the pressure in the reaction kettle drops significantly, gradually add the remaining Propylene oxide is placed in the reaction kettle. After the reaction is completed, the unreacted propy...
Embodiment 1
[0034] 100 parts by weight of polyether ester polyol (M n =2000) for vacuum dehydration, cooled to 55°C, added 8.77 parts by weight of toluene-2,4-diisocyanate (TDI), slowly raised the temperature to 80°C, and kept the temperature for 1 hour to prepare a polyurethane preform with an NCO mass fraction of 3.5%. Polymer. Weigh the polyurethane prepolymer and heat it to 80°C, add 10.903 parts by weight of chain extender to melt 3,3'-dichloro-4,4'-diaminodiphenylmethane (MOCA) according to the chain extension coefficient of 0.90, and stir rapidly Evenly, pour it into a preheated mold, pressurize and vulcanize it on a flat vulcanizing machine under the conditions of 8MPa and 100°C, put the test piece in an oven at 100°C after demoulding, and vulcanize for 8 hours to obtain a polyether ester polyurethane elastomer.
Embodiment 2
[0036] 100 parts by weight of polyether ester polyol (M n =2000) for vacuum dehydration, cooled to 55°C, added 8.79 parts by weight of toluene-2,4-diisocyanate (TDI), slowly raised the temperature to 80°C, and kept the temperature for 1 hour to prepare a polyurethane preform with an NCO mass fraction of 4.0%. Polymer. Weigh the polyurethane prepolymer and heat it to 80°C, add 12.45 parts by weight of chain extender to melt 3,3'-dichloro-4,4'-diaminodiphenylmethane (MOCA) according to the chain extension coefficient of 0.90, and stir rapidly Evenly, pour it into a preheated mold, pressurize and vulcanize it on a flat vulcanizing machine under the conditions of 8MPa and 100°C, put the test piece in an oven at 100°C after demoulding, and vulcanize for 8 hours to obtain a polyether ester polyurethane elastomer.
PUM
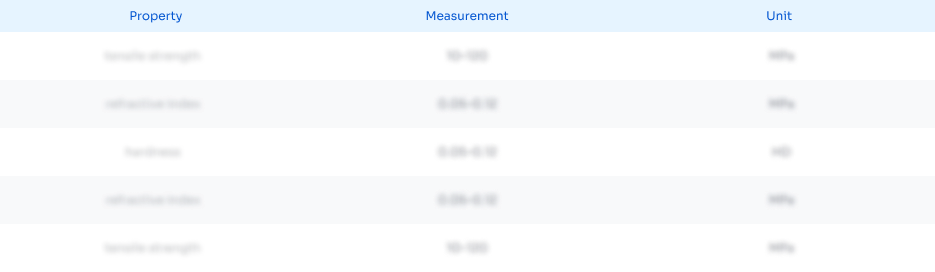
Abstract
Description
Claims
Application Information

- R&D
- Intellectual Property
- Life Sciences
- Materials
- Tech Scout
- Unparalleled Data Quality
- Higher Quality Content
- 60% Fewer Hallucinations
Browse by: Latest US Patents, China's latest patents, Technical Efficacy Thesaurus, Application Domain, Technology Topic, Popular Technical Reports.
© 2025 PatSnap. All rights reserved.Legal|Privacy policy|Modern Slavery Act Transparency Statement|Sitemap|About US| Contact US: help@patsnap.com