Design method of magnetic latching parallel-stepping, rotating and swinging extensible joint
A design method and magnetic retention technology, applied in the direction of electromagnet, motor generator control, electromagnet with armature, etc., can solve the problems of only turning, robot failure, liquid leakage and other problems
- Summary
- Abstract
- Description
- Claims
- Application Information
AI Technical Summary
Problems solved by technology
Method used
Image
Examples
Embodiment Construction
[0006]The magnetically held parallel step rotary swing telescopic joint works under the action of the processor and the encoder. When the processor gives a positive pulse voltage to a certain unit in the magnetically held parallel stepping driver, or to the Keep a positive pulse voltage of the unit magnetic holding driver on the parallel stepping rotary disk, and pass through the peripheral circuit, it will give the unit magnetic holding driver a positive pulse current, the unit magnetic holding driver will move forward, the encoder It will record the state of the magnetic holding drive of this unit. When the processor gives a reverse voltage to a certain unit magnetic holding drive in the magnetic holding parallel stepping drive, or a magnetic holding drive to a unit on the magnetic holding parallel stepping rotary disk The reverse pulse voltage, through the peripheral circuit, will give the unit magnetic holding driver a reverse pulse current, the unit magnetic holding driver...
PUM
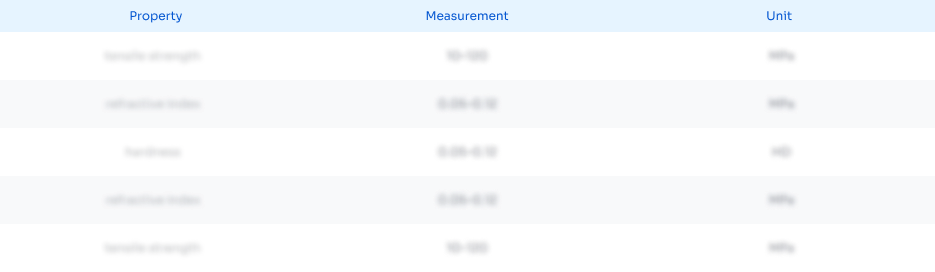
Abstract
Description
Claims
Application Information

- R&D
- Intellectual Property
- Life Sciences
- Materials
- Tech Scout
- Unparalleled Data Quality
- Higher Quality Content
- 60% Fewer Hallucinations
Browse by: Latest US Patents, China's latest patents, Technical Efficacy Thesaurus, Application Domain, Technology Topic, Popular Technical Reports.
© 2025 PatSnap. All rights reserved.Legal|Privacy policy|Modern Slavery Act Transparency Statement|Sitemap|About US| Contact US: help@patsnap.com