Method for analyzing magnetic roasting effects of iron ore having different granularity ranges
A particle size range, magnetization roasting technology, applied in the field of metallurgy, can solve problems such as large volume capacity, loss, and many influencing factors, and achieve the effects of high experimental accuracy, improved resource utilization, and fewer external influencing factors.
- Summary
- Abstract
- Description
- Claims
- Application Information
AI Technical Summary
Problems solved by technology
Method used
Examples
Embodiment 1
[0020] A method for analyzing the effect of iron ore magnetization roasting in different particle size ranges, comprising the following specific steps:
[0021] (1) Raw material preparation
[0022] The refractory iron ore produced by JISCO Jingtieshan Mine is selected as the raw material iron ore, and its properties are: TFe: 35.00%, FeO: 8.62%, SiO 2 : 22.34%; take 70kg of raw material iron ore of 0~15mm, use the quartering method to gradually divide and take 5kg of iron ore for later use, and then use the quartering method to gradually reduce and divide the above 5kg iron ore to take 1kg as Mineral sample for experiment; put the coal for reduction into a vibrating mill and grind it to less than 1mm to obtain a coal sample for reduction. The properties of the coal sample are moisture: 14.8%, ash: 23.12%, volatile matter: 31.21%, fixed carbon: 52.06 %;
[0023] (2) Drying: Dry the ore sample with a large multi-purpose drying box model DGT202, the drying temperature is 1...
Embodiment 2
[0037] The difference between embodiment 2 and embodiment 1 is:
[0038] In step (1), the raw iron ore of 65kg is sampled;
[0039] In step (2), the weight of the ore sample after drying is 0.953kg;
[0040] In step (3), the mass proportion of the coal sample in the mixture is 4%, the roasting temperature is 900°C, and the roasting time is 50 minutes;
[0041] In step (6), the mass of the dried roasted ore is 0.8537kg, and the burning loss rate is 10.42%;
[0042] In step (7), the weight percentages of the roasted ore in the four particle size ranges of 0~1mm, 1~3mm, 3~5mm and 5~15mm are respectively: 36.13%, 15.17%, 14.44%, 34.26%;
[0043] In step (9), the magnetic separation field strength is 1500Oe.
[0044] The experimental results are as follows:
[0045] The roasted ore grade of 0~1mm is 40.23%, the magnetic susceptibility is 1.73, the grade of iron concentrate is 55.43%, the yield is 52.74%, and the metal recovery rate is 72.67%;
[0046] The grade of 1~3mm roaste...
Embodiment 3
[0050] The difference between embodiment 3 and embodiment 1 is:
[0051] In step (1), 60kg of raw iron ore is taken for sampling;
[0052] In step (2), the weight of the ore sample after drying is 0.950kg;
[0053] In step (3), the mass proportion of the coal sample in the mixture is 5%, the roasting temperature is 800°C, and the roasting time is 65 minutes;
[0054] In step (6), the mass of the dried roasted ore is 0.8774kg, and the loss rate is 7.64%; The weight percentages of ore are: 35.22%, 14.79%, 16.02%, 33.97%;
[0055] In step (9), the magnetic separation field strength is 1000Oe.
[0056] The experimental results are as follows:
[0057] The roasted ore grade of 0~1mm is 38.49%, the magnetic susceptibility is 1.99, the grade of iron concentrate is 55.37%, the yield is 53.46%, and the metal recovery rate is 77.16%;
[0058] The grade of 1~3mm roasted ore is 40.59%, the magnetic susceptibility is 2.38, the grade of iron concentrate is 58.79%, the yield is 61.33%, ...
PUM
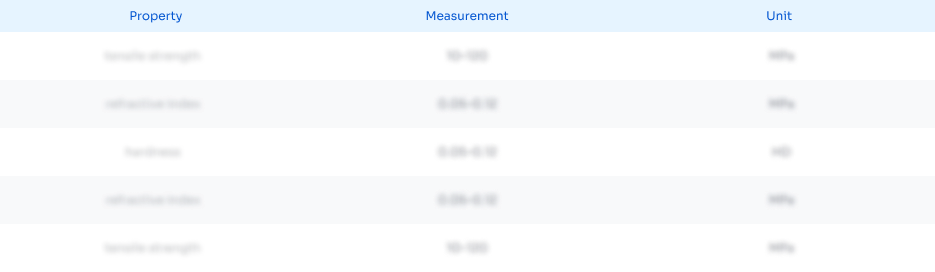
Abstract
Description
Claims
Application Information

- R&D
- Intellectual Property
- Life Sciences
- Materials
- Tech Scout
- Unparalleled Data Quality
- Higher Quality Content
- 60% Fewer Hallucinations
Browse by: Latest US Patents, China's latest patents, Technical Efficacy Thesaurus, Application Domain, Technology Topic, Popular Technical Reports.
© 2025 PatSnap. All rights reserved.Legal|Privacy policy|Modern Slavery Act Transparency Statement|Sitemap|About US| Contact US: help@patsnap.com