Preparation method of dry gas hydrogen production preconversion catalyst
A catalyst and pre-conversion technology, applied in physical/chemical process catalysts, metal/metal oxide/metal hydroxide catalysts, chemical instruments and methods, etc., can solve the problems of low-temperature reduction performance, poor low-temperature activity, and good performance
- Summary
- Abstract
- Description
- Claims
- Application Information
AI Technical Summary
Problems solved by technology
Method used
Image
Examples
Embodiment 1
[0015] The weight ratio of each component of the prereforming catalyst in this embodiment is shown in Table 1 below:
[0016] Table 1 Embodiment 1 catalyst composition
[0017] components
NiO
MgO
Al 2 o 3
La 2 o 3
MO X
Proportion
35
15
45
2
3
[0018] (1) Preparation of reactant raw materials:
[0019] A. First, weigh 18g of aluminum hydroxide and 3g of heavy magnesium oxide, perform ball milling and mixing for 1.5hr-2hr, and then roast at a high temperature of 1100°C-1300°C for 2hr-4hr to prepare the carrier.
[0020] B, 260g / L Ni(NO 3 ) 2 Solution 25ml, M(NO 3 ) x (M is one or more of Zr, Y, Ag, Co, Cu, Zn, K) salt 1.8g, 360g / L La(NO 3 ) 2 Solution 1.2ml, the three solutions are mixed for use;
[0021] C. Na 2 CO 3 Solution configuration: saturated sodium carbonate solution for use.
[0022] (2) Neutralize precipitation:
[0023] A. In a water bath at 40°C±5°C, add the B and C solu...
Embodiment 2
[0035] The weight ratio of each component of the prereforming catalyst in this embodiment is shown in Table 2 below:
[0036] Table 2 Embodiment 2 catalyst composition
[0037] components
NiO
MgO
Al 2 o 3
La 2 o 3
MO X
Proportion
40
10
45
2
3
[0038] (1) Preparation of reactant raw materials:
[0039] A. First, weigh 18g of aluminum hydroxide and 2g of heavy magnesium oxide, perform ball milling and mixing for 1.5hr-2hr, and then roast at a high temperature of 1100°C-1300°C for 2hr-4hr to prepare the carrier.
[0040] B, 260g / L Ni(NO 3 ) 2 Solution 30ml, M(NO 3 ) x Salt 1.8g, 360g / L La(NO 3 ) 2 Solution 1.2ml, the three solutions are mixed for use;
[0041] C. Na 2 CO 3 Solution configuration: saturated sodium carbonate solution for use.
[0042] (2) Neutralize precipitation:
[0043]A. In a water bath at 40°C±5°C, add the B and C solutions configured in (1) into the reactor side-by...
Embodiment 3
[0055] The weight ratio of each component of the prereforming catalyst in this embodiment is shown in the following table 3:
[0056] Table 3 Embodiment 3 Catalyst Composition
[0057] components
NiO
MgO
Al 2 o 3
La 2 o 3
MO X
Proportion
45
10
40
2
3
[0058] (1) Preparation of reactant raw materials:
[0059] A. First, weigh 12g of aluminum hydroxide and 2g of heavy magnesium oxide, perform ball milling and mixing for 1.5hr-2hr, and then roast at a high temperature of 1100°C-1300°C for 2hr-4hr to prepare the carrier.
[0060] B, 260g / L Ni(NO 3 ) 2 Solution 40ml, M(NO 3 ) x Salt 1.8g, 360g / L La(NO 3 ) 2 Solution 1.2ml, the three solutions are mixed for use;
[0061] C. Na 2 CO 3 Solution configuration: saturated sodium carbonate solution for use.
[0062] (2) Neutralize precipitation:
[0063] A. In a water bath at 40°C±5°C, add the B and C solutions configured in (1) into the reacto...
PUM
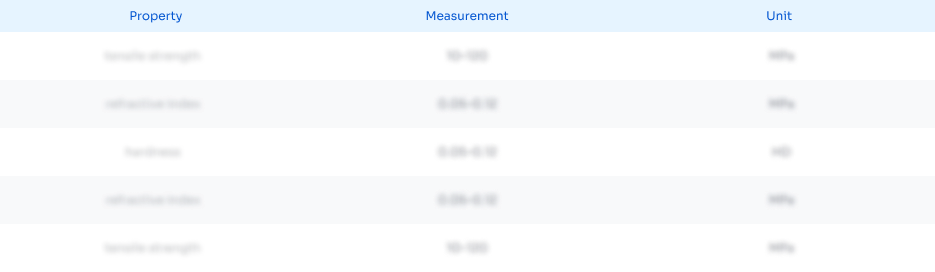
Abstract
Description
Claims
Application Information

- R&D
- Intellectual Property
- Life Sciences
- Materials
- Tech Scout
- Unparalleled Data Quality
- Higher Quality Content
- 60% Fewer Hallucinations
Browse by: Latest US Patents, China's latest patents, Technical Efficacy Thesaurus, Application Domain, Technology Topic, Popular Technical Reports.
© 2025 PatSnap. All rights reserved.Legal|Privacy policy|Modern Slavery Act Transparency Statement|Sitemap|About US| Contact US: help@patsnap.com