High-resilience urethane elastic fiber as well as preparation method thereof
A spandex fiber and high-resilience technology, which is applied in the field of preparation of high-resilience spandex fiber, can solve the problems of inconspicuous effect, unstable storage of spinning solution, and affecting production stability, etc., and achieves low cost, easy industrial implementation, Ease of promotion
- Summary
- Abstract
- Description
- Claims
- Application Information
AI Technical Summary
Problems solved by technology
Method used
Image
Examples
preparation example Construction
[0024] The preparation method of high resilience spandex fiber of the present invention comprises the following steps:
[0025] 1) Mix the raw materials polytetramethylene ether glycol PTMG and 4,4-diphenylmethane diisocyanate MDI, and react at 75-90°C for 100-120 minutes to prepare a prepolymer, wherein the molar ratio of MDI to PTMG is (1.80~2.00): 1;
[0026] 2) Prepare chain extender mixture solution: dissolve one or both of ethylenediamine and butylenediamine into the solvent N,N-dimethylacetamide DMAc to form a chain extender with a mass percentage concentration of 1.00-4.00%. Chain agent mixture solution;
[0027] 3) Add the prepolymer into the chain extender mixture solution and stir, wherein the molar ratio of amine to isocyanate is (0.90-0.98): 1, react to form a mass percent concentration 35-45% low molecular weight polyurethane solution;
[0028] 4) Add diethylenetriamine DETA to the low-molecular-weight polyurethane solution and stir, wherein the molar ratio of...
Embodiment 1
[0036] Step 1: Fabrication of Modified Attapulgite Nanorods
[0037] 1) At 70°C, add 4,4-diphenylmethane diisocyanate to the polyether diol, wherein the molar ratio of isocyanate to hydroxyl is 1.90:1; after 150 minutes of reaction, Diethylamine was added, wherein the molar ratio of secondary amino groups to isocyanate groups was 1.02:1 to obtain liquid polyurethane.
[0038] 2) Dry the nano-attapulgite at 120°C for 5 hours; place the treated nano-attapulgite in a stainless steel kettle, vacuumize to 0.01 standard atmospheric pressure, and the temperature is 70°C, inject liquid polyurethane into the stainless steel kettle to impregnate the nano Stir the attapulgite vigorously, apply an air pressure of 0.5MPa, and keep the pressure for 1.5 hours, wherein the mass ratio of liquid polyurethane to nano-attapulgite is 6:1.
[0039] Step 2: Manufacture of Fiber-Forming Polymer
[0040] 1) Mix raw materials polytetramethylene ether glycol (PTMG) and 4,4-diphenylmethane diisocyanate...
Embodiment 2
[0051] Step 1: Fabrication of Modified Attapulgite Nanorods
[0052] 1) At 70°C, add 4,4-diphenylmethane diisocyanate to the polyether diol, wherein the molar ratio of isocyanate to hydroxyl is 1.90:1; after 150 minutes of reaction, Diethylamine was added, wherein the molar ratio of secondary amino groups to isocyanate groups was 1.02:1 to obtain liquid polyurethane.
[0053] 2) Dry the nano-attapulgite at 120°C for 5 hours; place the treated nano-attapulgite in a stainless steel kettle, vacuumize to 0.01 standard atmospheric pressure, and the temperature is 70°C, inject liquid polyurethane into the stainless steel kettle to impregnate the nano Stir the attapulgite vigorously, apply an air pressure of 0.5 MPa, and keep the pressure for 1.5 hours, wherein the mass ratio of liquid polyurethane to nano-attapulgite is 5:1.
[0054] Step 2: Manufacture of Fiber-Forming Polymer
[0055] 1) Mix raw materials polytetramethylene ether glycol (PTMG) and 4,4-diphenylmethane diisocyanat...
PUM
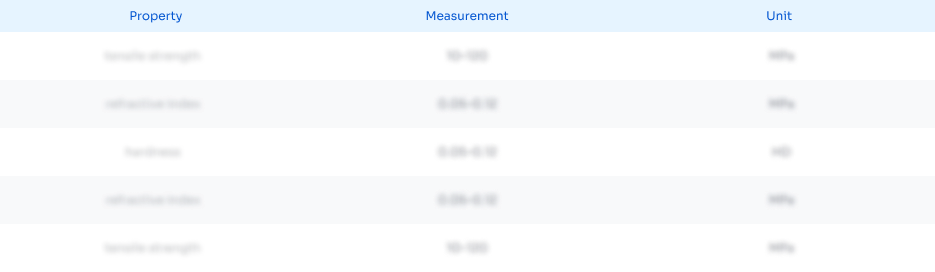
Abstract
Description
Claims
Application Information

- R&D
- Intellectual Property
- Life Sciences
- Materials
- Tech Scout
- Unparalleled Data Quality
- Higher Quality Content
- 60% Fewer Hallucinations
Browse by: Latest US Patents, China's latest patents, Technical Efficacy Thesaurus, Application Domain, Technology Topic, Popular Technical Reports.
© 2025 PatSnap. All rights reserved.Legal|Privacy policy|Modern Slavery Act Transparency Statement|Sitemap|About US| Contact US: help@patsnap.com