Method for preparing dimethyl ether through methanol dehydration
A methanol dehydration and dimethyl ether technology, applied in the dehydration of hydroxyl-containing compounds to prepare ether, ether preparation, organic chemistry, etc., can solve the problems of serious equipment corrosion, serious environmental pollution, and harsh operating conditions, and achieve high operating flexibility. Simple process and high conversion rate
- Summary
- Abstract
- Description
- Claims
- Application Information
AI Technical Summary
Problems solved by technology
Method used
Image
Examples
Embodiment 1
[0023] Such as figure 1 As shown, 500kg / h of methanol with a content of 99.5% (mass ratio) enters the first heat exchanger 2 through the methanol feed pipe 1, and passes through the outlet pipe 3 of the first methanol heat exchanger after heat exchange, and the temperature is 50-60°C , into the second heat exchanger 4 for heat exchange, and then through the second heat exchanger outlet pipe 5, the temperature is 70 ~ 80 ° C, enters the heater 6, the heated methanol passes through the heater outlet pipe 7, the temperature is 140 ~ 150°C, enter dehydration reactor 8, operating pressure: 1.5-3.0MPa, operating temperature: 140-150°C, space velocity: 1h - , under the action of a catalyst, methanol is dehydrated to generate a dimethyl ether mixture, and the resulting reaction mixture enters the gas-liquid separator 10 through the outlet pipe 9 of the dehydration reactor, the operating pressure is 0.8-1.3 MPa, and the operating temperature is 120-130 ° C. The gas phase directly ente...
Embodiment 2
[0025] Such as figure 2 As shown, 500kg / h of methanol with a content of 99.5% (mass ratio) enters the first heat exchanger 2 through the methanol feed pipe 1, and passes through the outlet pipe 3 of the first methanol heat exchanger after heat exchange, and the temperature is 40-50°C , enter the second heat exchanger 4 for heat exchange, and then pass through the second heat exchanger outlet pipe 5, the temperature is 60 ~ 70 ° C, enter the heater 6, the heated methanol passes through the heater outlet pipe 7, the temperature is 120 ~ 130°C, enter dehydration reactor 8, operating pressure: 3.0-4.0MPa, operating temperature: 120-130°C, space velocity: 5h -, under the action of a catalyst, methanol is dehydrated to generate a dimethyl ether mixture, and the resulting reaction mixture enters the gas-liquid separator 10 through the outlet pipe 9 of the dehydration reactor, the operating pressure: 1.3-1.5MPa, and the operating temperature is 110-120°C, and the separation is obtain...
Embodiment 3
[0027] Such as figure 1 As shown, 500kg / h of methanol with a content of 99.5% (mass ratio) enters the first heat exchanger 2 through the methanol feed pipe 1, and passes through the outlet pipe 3 of the first methanol heat exchanger after heat exchange, and the temperature is 50-60°C , enter the second heat exchanger 4 for heat exchange, and then pass through the second heat exchanger outlet pipe 5, the temperature is 70 ~ 80 ° C, enter the heater 6, the heated methanol passes through the heater outlet pipe 7, the temperature is 150 ~ 160°C, enter dehydration reactor 8, operating pressure: 0.5-1.5MPa, operating temperature: 150-160°C, space velocity: 3h - , under the action of a catalyst, methanol is dehydrated to form a dimethyl ether mixture, and the resulting reaction mixture enters the gas-liquid separator 10 through the outlet pipe 9 of the dehydration reactor, the operating pressure: 0.5-0.8MPa, and the operating temperature is 140-150°C, and the obtained The gas phase ...
PUM
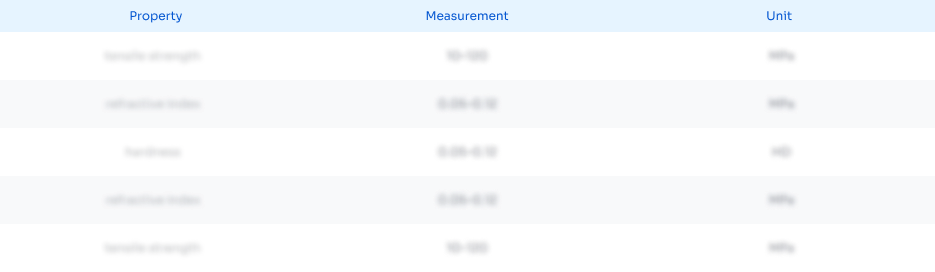
Abstract
Description
Claims
Application Information

- R&D
- Intellectual Property
- Life Sciences
- Materials
- Tech Scout
- Unparalleled Data Quality
- Higher Quality Content
- 60% Fewer Hallucinations
Browse by: Latest US Patents, China's latest patents, Technical Efficacy Thesaurus, Application Domain, Technology Topic, Popular Technical Reports.
© 2025 PatSnap. All rights reserved.Legal|Privacy policy|Modern Slavery Act Transparency Statement|Sitemap|About US| Contact US: help@patsnap.com