Monofilament filter fabric for coal washing and preparation method thereof
A monofilament and filter cloth technology, which is applied in the field of monofilament filter cloth for coal washing and its preparation, can solve the problems of reducing loom production efficiency, increasing production cost, and reducing production efficiency, and achieves improved external appearance, extended service life, The effect of improving productivity
- Summary
- Abstract
- Description
- Claims
- Application Information
AI Technical Summary
Problems solved by technology
Method used
Image
Examples
Embodiment 1-4
[0042] Table 2 embodiment 1-4 prepares the technological condition of monofilament filter cloth
[0043]
[0044]
[0045] The monofilament strength of the high-density polyethylene and polypropylene blended provided by Examples 1-4 can reach 59-63cN / tex, and the monofilament breakage will not occur when it is used for weaving, and the loom can be produced smoothly. Compared with polypropylene monofilament weaving, the production efficiency of the loom is greatly improved and the production cost is reduced.
[0046] The material, weight and breaking strength of the monofilament filter cloth for coal washing provided in Examples 5-8 are shown in Table 3.
[0047] The material, weight and breaking strength of the monofilament filter cloth for coal washing provided by table 3 embodiment 5-8
[0048]
[0049]
Embodiment 5-8
[0051] Table 4 embodiment 5-8 prepares the technological condition of monofilament filter cloth
[0052]
[0053]
[0054] The monofilament strength of high-density polyethylene and polypropylene blended provided by Examples 5-8 can reach 60-63cN / tex, and the situation of monofilament breakage will not occur when using it for weaving, and the loom can be produced smoothly. Compared with polypropylene monofilament weaving, the production efficiency of the loom is greatly improved and the production cost is reduced; at the same time, the monofilament filter cloth is green, which makes the surface of the filter cloth better and more attractive to consumers.
[0055] The material, weight and breaking strength of the monofilament filter cloth for coal washing provided in Examples 9-12 are shown in Table 5.
[0056] The material, weight and breaking strength of the monofilament filter cloth for coal washing provided by table 5 embodiment 9-12
[0057]
[0058]
Embodiment 9-12
[0060] Table 6 embodiment 9-12 prepares the technological condition of monofilament filter cloth
[0061]
[0062]
[0063] The monofilament strength of the high-density polyethylene and polypropylene blended provided by Examples 9-12 can reach 60-63cN / tex, and the monofilament breakage will not occur when using it for weaving, and the loom can be produced smoothly. Compared with the monofilament weaving made of polypropylene material, the production efficiency of the loom is greatly improved, and the production cost is reduced; meanwhile, in Examples 9-12, the matting agent can choose titanium dioxide and other substances that can whiten. Using matting agent as one of the raw materials to produce monofilament filter cloth can improve the optical reflection performance of the monofilament filter cloth surface, reduce the transparency of the monofilament filter cloth, and increase the whiteness of the monofilament filter cloth. The resulting monofilament filter cloth has ...
PUM
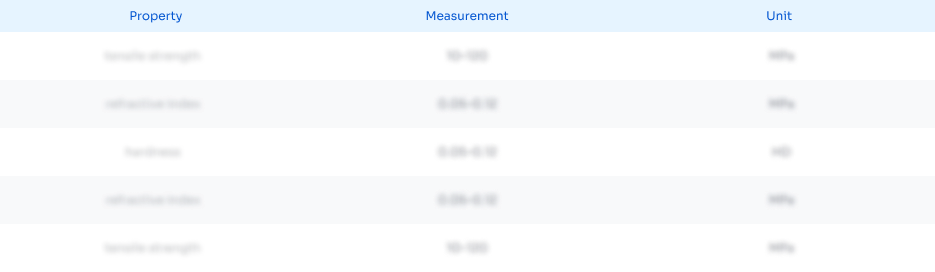
Abstract
Description
Claims
Application Information

- R&D
- Intellectual Property
- Life Sciences
- Materials
- Tech Scout
- Unparalleled Data Quality
- Higher Quality Content
- 60% Fewer Hallucinations
Browse by: Latest US Patents, China's latest patents, Technical Efficacy Thesaurus, Application Domain, Technology Topic, Popular Technical Reports.
© 2025 PatSnap. All rights reserved.Legal|Privacy policy|Modern Slavery Act Transparency Statement|Sitemap|About US| Contact US: help@patsnap.com