Processing method of wastewater of acrylonitrile production refining process
A technology for wastewater treatment and acrylonitrile, which is applied in natural water treatment, oxidized water/sewage treatment, water/sludge/sewage treatment, etc., can solve the problems of complex treatment process and high operating cost, and achieve simple process and low operating cost. , remove the effect completely
- Summary
- Abstract
- Description
- Claims
- Application Information
AI Technical Summary
Problems solved by technology
Method used
Image
Examples
Embodiment 1
[0016] RuCl containing 1.5 g of ruthenium 3 and PdCl with 0.5 g of palladium 2 Dissolve in 30ml distilled water to make a solution , the solution Add dropwise to 98 g of TiO with constant stirring 2 In the carrier, the catalyst precursor is prepared ; Catalyst precursor Dry at 100°C for 12 hours and calcined at 600°C for 5 hours to obtain catalyst precursor II; catalyst precursor II was reduced with excess hydrazine hydrate and dried at 120°C for 12 hours to obtain catalyst Pd 0.5 Ru 1.5 (TiO 2 ) 98 .
[0017] The waste water from the acrylonitrile production and refining system is mixed with the gas containing elemental oxygen and passed through the wet oxidation reactor. The reaction conditions are shown in Table 1. After the reaction, the waste water is cooled to room temperature by a cooler and separated from the gas and liquid. The COD value of the waste water before the reaction and the value after the reaction are analyzed. See Table 2 for the COD value of ...
Embodiment 2~9
[0020] The preparation process of the catalyst is the same as in Example 1, except that different amounts or types of precious metals and supports and different preparation conditions are used. The specific composition is shown in Table 1. The catalyst activity evaluation results are shown in Table 2.
[0021]
PUM
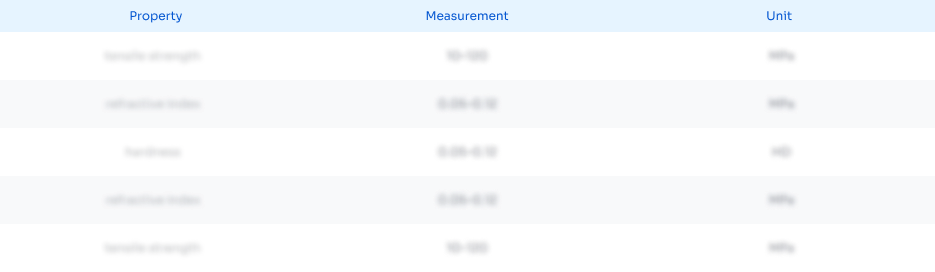
Abstract
Description
Claims
Application Information

- R&D
- Intellectual Property
- Life Sciences
- Materials
- Tech Scout
- Unparalleled Data Quality
- Higher Quality Content
- 60% Fewer Hallucinations
Browse by: Latest US Patents, China's latest patents, Technical Efficacy Thesaurus, Application Domain, Technology Topic, Popular Technical Reports.
© 2025 PatSnap. All rights reserved.Legal|Privacy policy|Modern Slavery Act Transparency Statement|Sitemap|About US| Contact US: help@patsnap.com