Coking ammonium sulphate front part gas pipeline pressure welding method
A gas pipeline, coking sulfur technology, applied in welding equipment, metal processing equipment, manufacturing tools, etc., can solve the problem of not being able to weld large areas of corrosion and leakage of gas pipelines, and achieve the effect of reducing daily special care costs
- Summary
- Abstract
- Description
- Claims
- Application Information
AI Technical Summary
Problems solved by technology
Method used
Image
Examples
Embodiment
[0050] For a schematic diagram of this embodiment, see figure 1 , this embodiment includes the following steps in sequence:
[0051] Ⅰ , control oxygen content
[0052]From the coke oven, rising pipe, gas collecting pipe, electric tar catcher to the entire negative pressure operation area of the blower, the gas pipeline 1 with an outer diameter of 1.6 meters and a length of 100 meters ensures that the gas pipeline 1 and the connecting pipeline are sealed with the outside world. Reduce the coal loading time, coke pushing time, and close the observation hole to clean the hole to strictly control the air inhaled into the negative pressure area, so as to effectively control the oxygen content in the gas; the oxygen content in the negative pressure operation area cannot exceed the limit, and the oxygen content is not more than 2%. An abnormality should be checked and ruled out in time.
[0053] Ⅱ , to ensure blower pressure
[0054] Strictly ensure the stable operation of th...
PUM
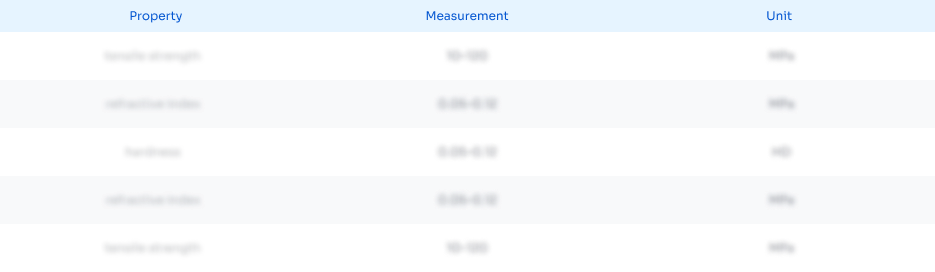
Abstract
Description
Claims
Application Information

- R&D Engineer
- R&D Manager
- IP Professional
- Industry Leading Data Capabilities
- Powerful AI technology
- Patent DNA Extraction
Browse by: Latest US Patents, China's latest patents, Technical Efficacy Thesaurus, Application Domain, Technology Topic, Popular Technical Reports.
© 2024 PatSnap. All rights reserved.Legal|Privacy policy|Modern Slavery Act Transparency Statement|Sitemap|About US| Contact US: help@patsnap.com