Preparation method of hydrophobic lignosulfonate
A technology of lignosulfonate and hydrophobicity, which is applied in the surface treatment of lignosulfonate and the preparation of hydrophobic lignosulfonate, can solve the problems of resource waste, reduce moisture absorption, and achieve stable and reliable reaction , The effect of improving lipophilicity
- Summary
- Abstract
- Description
- Claims
- Application Information
AI Technical Summary
Problems solved by technology
Method used
Examples
Embodiment 1
[0022] A preparation method of hydrophobic calcium lignosulfonate;
[0023] ①Dissolution: Grind calcium lignosulfonate to a particle size of 300-500nm, dry in vacuum at 110°C for 12 hours, weigh 5g of crushed and dried calcium lignosulfonate, mix with 100ml of deionized water, and stir at 160°C for 1h .
[0024] ②Grafting: Add 0.1g of tris(dioctylpyrophosphoryloxy)isopropyl titanate coupling agent to the aqueous solution of calcium lignosulfonate and mix well, react at 170°C for 6h, then let stand for 12h, suction filter, After vacuum drying for 12 hours, disperse in 20ml of acetone, let stand for 12 hours, filter with suction, wash, and vacuum dry at 110°C for 12 hours.
[0025] It was measured that within 12 hours, the moisture absorption rate decreased by 5.95%, and the oil absorption rate increased by 49.52%. After 36 hours, the calcium lignosulfonate had a constant weight.
Embodiment 2
[0027] The difference with embodiment 1 is:
[0028] The titanate coupling agent is diisostearyl ethylene glycol titanate coupling agent, and its mass is 0.15 g.
[0029] It was measured that within 12 hours, the moisture absorption rate decreased by 6.28%, the oil absorption rate increased by 52.39%, and the calcium lignosulfonate had a constant weight after 36 hours.
Embodiment 3
[0031] The difference with embodiment 1 is:
[0032] The titanate coupling agent is bis(dioctyl pyrophosphate) glycolate coupling agent, and its mass is 0.175g.
[0033] It was measured that within 12 hours, the moisture absorption rate decreased by 6.97%, the oil absorption rate increased by 54.03%, and the calcium lignosulfonate had a constant weight after 24 hours.
PUM
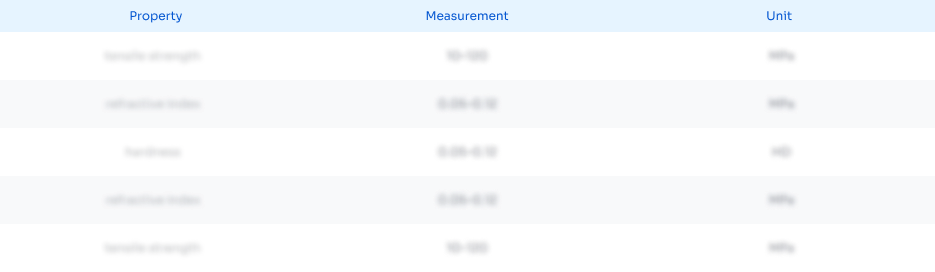
Abstract
Description
Claims
Application Information

- Generate Ideas
- Intellectual Property
- Life Sciences
- Materials
- Tech Scout
- Unparalleled Data Quality
- Higher Quality Content
- 60% Fewer Hallucinations
Browse by: Latest US Patents, China's latest patents, Technical Efficacy Thesaurus, Application Domain, Technology Topic, Popular Technical Reports.
© 2025 PatSnap. All rights reserved.Legal|Privacy policy|Modern Slavery Act Transparency Statement|Sitemap|About US| Contact US: help@patsnap.com