System and method for forecasting molten steel components in RH refining process in online manner
A technology of molten steel composition and refining process, applied in the system field of online prediction of molten steel composition in the RH refining process, can solve the problems of high cost, lack of accurate analysis, and vacuum degassing, etc., achieve high degree of automation and reduce labor intensity , to ensure the effect of reasonableness and accuracy
- Summary
- Abstract
- Description
- Claims
- Application Information
AI Technical Summary
Problems solved by technology
Method used
Image
Examples
Embodiment Construction
[0050] The specific implementation manners of the present invention will be described in detail below in conjunction with the accompanying drawings.
[0051] as attached figure 1 As shown, the system for online prediction of molten steel composition in the RH refining process of this embodiment includes: an information acquisition module 1, which is used to obtain the amount of molten steel, molten steel composition, steel target composition, alloy composition, alloy yield of the corresponding composition, and Corresponding silo number; degassing judging module 2, judging whether the molten steel needs to be degassed, if necessary, the system sends instructions to the degassing module for degassing processing, if not, the system sends instructions to the gas content display module; Degassing module 3, degassing the molten steel according to the composition of the incoming molten steel and the smelting target requirements of the steel type; gas content comparison module 4, comp...
PUM
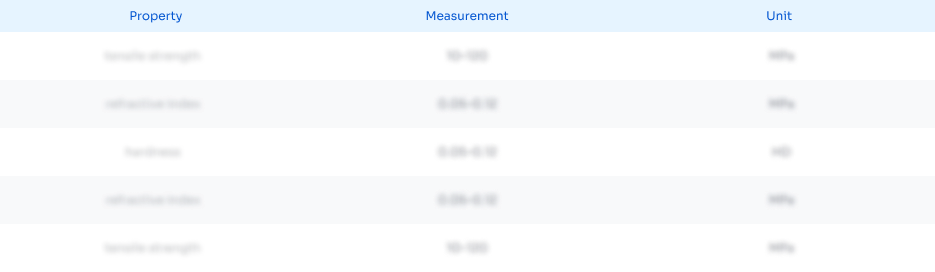
Abstract
Description
Claims
Application Information

- R&D Engineer
- R&D Manager
- IP Professional
- Industry Leading Data Capabilities
- Powerful AI technology
- Patent DNA Extraction
Browse by: Latest US Patents, China's latest patents, Technical Efficacy Thesaurus, Application Domain, Technology Topic, Popular Technical Reports.
© 2024 PatSnap. All rights reserved.Legal|Privacy policy|Modern Slavery Act Transparency Statement|Sitemap|About US| Contact US: help@patsnap.com