Preservative resin coating
An anti-corrosion resin and coating technology, applied in anti-corrosion coatings, coatings, etc., can solve the problems of fading and peeling, easy foaming, corrosion resistance and poor adhesion stability, etc., to increase anti-corrosion performance, adhesion, and use effect. Good, stable quality effect
- Summary
- Abstract
- Description
- Claims
- Application Information
AI Technical Summary
Problems solved by technology
Method used
Image
Examples
Embodiment 1
[0019] An anticorrosive resin coating whose components are composed of the following components in weight percentage: 60% of component A and 40% of component B;
[0020] The component A includes the following components in parts by weight: 50 parts polyester resin, 14 parts epoxy resin, 8 parts titanium dioxide, 5 parts barium metaborate, 5 parts talc, 0.5 parts auxiliary, 5 parts mixed Solvent; the mixed solvent is composed of xylene and butyl acetate, the volume ratio of xylene and butyl acetate in the mixed solvent is 4:1; the auxiliary agent is composed of defoamer, anti-settling agent and thixotropic agent ; The additives include defoamers, anti-settling agents and thixotropic agents in a weight ratio of 1:1:2
[0021] The B component includes the following components in parts by weight: 1 part of dibutyl phthalate, 3 parts of tricarboxymethyl propane, 15 parts of toluene diisocyanate, 1 part of cyclohexanone, 0.5 part of polyurethane dehydrating agent.
[0022] The preparation...
Embodiment 2
[0027] An anticorrosive resin coating whose components are composed of the following components by weight percentage: 80% of component A and 20% of component B;
[0028] The A component includes the following components in parts by weight: 40 parts polyester resin, 19 parts epoxy resin, 12 parts carbon black, 10 parts aluminum tripolyphosphate, 7 parts precipitated barium sulfate and mica powder, 2 parts auxiliary Agent, 15 parts of mixed solvent; the volume ratio of xylene to butyl acetate in the mixed solvent is 4:1; the weight ratio of the auxiliary agent including defoamer, anti-settling agent and thixotropic agent is 1:1:2 ;
[0029] The B component includes the following components in parts by weight: 0.5 parts of dioctyl phthalate, 8 parts of tricarboxymethyl propane, 25 parts of toluene diisocyanate, 3 parts of cyclohexanone, and 2 parts of polyurethane dehydrating agent.
[0030] The preparation method of the above anticorrosive resin coating includes the following steps:
...
Embodiment 3
[0035] An anticorrosive resin coating whose components are composed of the following components by weight percentage: 70% of component A and 30% of component B;
[0036] The component A includes the following components in parts by weight: 45 parts polyester resin, 16 parts epoxy resin, 10 parts phthalocyanine blue, 8 parts zinc molybdate, 6 parts natural barite powder, 1 part auxiliary, 10 parts mixed solvent; the volume ratio of xylene to butyl acetate in the mixed solvent is 4:1; the weight ratio of the auxiliary agent including defoamer, anti-settling agent and thixotropic agent is 1:1:2;
[0037] The B component includes the following components in parts by weight: 0.8 parts of dioctyl phthalate and dibutyl phthalate, 6 parts of tricarboxymethyl propane, 20 parts of toluene diisocyanate, 2 parts of cyclohexane Ketone, 1 part polyurethane dehydrating agent.
[0038] The preparation method of the above anticorrosive resin coating includes the following steps:
[0039] (1) Preparat...
PUM
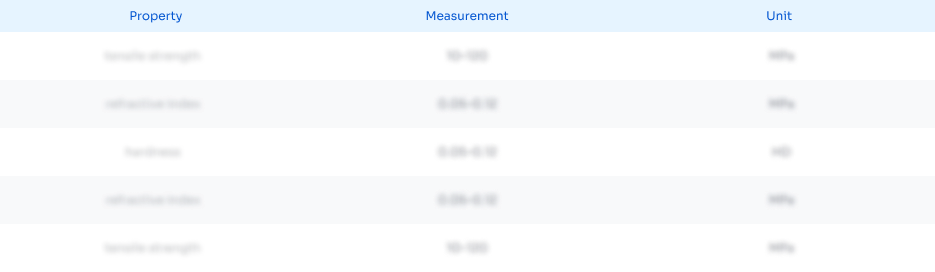
Abstract
Description
Claims
Application Information

- Generate Ideas
- Intellectual Property
- Life Sciences
- Materials
- Tech Scout
- Unparalleled Data Quality
- Higher Quality Content
- 60% Fewer Hallucinations
Browse by: Latest US Patents, China's latest patents, Technical Efficacy Thesaurus, Application Domain, Technology Topic, Popular Technical Reports.
© 2025 PatSnap. All rights reserved.Legal|Privacy policy|Modern Slavery Act Transparency Statement|Sitemap|About US| Contact US: help@patsnap.com