Humic acid composite material and preparation method thereof
A composite material and humic acid technology, applied in the field of humic acid composite material and its preparation, can solve the problems of complicated processing process, high cost, low utilization rate of humic acid, etc., and achieve the effect of broad industrial application prospect and convenient processing.
- Summary
- Abstract
- Description
- Claims
- Application Information
AI Technical Summary
Problems solved by technology
Method used
Image
Examples
Embodiment 1
[0023] A; soil humic acid, polylactic acid, and polybutylene succinate are dried, the drying temperature is 80°C, and the drying time is 5 hours;
[0024] B: Glycerin, phthalates, 2,6-di-tert-butyl-4-methylphenol and soil humic acid, polylactic acid, and polybutylene succinate after drying in step A were dried Stir evenly in a high-speed mixer, and then put it into an internal mixer for blending. The blending temperature is 160 ° C, the rotor speed is 60 rpm, and the blending time is 8 minutes to obtain a solid mixture; wherein the weight percentage of each component is as follows : Soil humic acid content is 40%, polylactic acid content is 30%, polybutylene succinate content is 21.5%, glycerin content is 5%, epoxy fatty acid ester content is 3%, 2,6-diol The content of tert-butyl-4-methylphenol is 0.5%;
[0025] C: The solid mixture is subjected to hot-compression composite molding on a hot press: the temperature is 160° C., the pressure is 15 MPa, and the time is 6 minutes ...
Embodiment 2
[0027] A; Coal sodium humate and polypropylene are dried, the drying temperature is 90°C, and the drying time is 4 hours;
[0028] B: Combine isocyanate crosslinking agent, aliphatic dibasic acid esters, stearic acid, β-(3,5-di-tert-butyl-4-hydroxyphenyl) propionate n-octadecyl alcohol with step A The dried coal sodium humate and polypropylene are stirred evenly in a dry high-speed mixer, and then put into an internal mixer for blending. The blending temperature is 180°C, the rotor speed is 50rpm, and the blending time is 25 minutes. , to obtain a solid mixture; wherein the weight percentages of each component are as follows: the content of coal sodium humate is 60%, the content of polypropylene is 16%, the content of isocyanate crosslinking agent is 8%, and the content of aliphatic dibasic acid esters The content of stearic acid is 7%, the content of stearic acid is 8%, and the content of β-(3,5-di-tert-butyl-4-hydroxyphenyl) n-octadecyl propionate is 1%;
[0029] C: The sol...
Embodiment 3
[0031] A: Drying bio-fermented humic acid, acrylonitrile / butadiene / styrene copolymer, polycarbonate, and polyamide, the drying temperature is 55°C, and the drying time is 12 hours;
[0032]B: Combine citrates, oleamide, N,N'-bis-(3-(3,5-di-tert-butyl-4-hydroxyphenyl)propionyl)hexamethylenediamine with the dried Biologically fermented humic acid, acrylonitrile / butadiene / styrene copolymer, polycarbonate, and polyamide are stirred evenly in a dry high-speed mixer, and then put into an internal mixer for blending. The blending temperature is 230°C, and the rotor The rotation speed was 140rpm, and the blending time was 5 minutes to obtain a solid mixture; wherein the weight percentages of each component were as follows: the content of bio-fermented humic acid was 30%, and the content of acrylonitrile / butadiene / styrene copolymer was 25%. , the polycarbonate content is 20%, the polyamide content is 15.5%, the citrate content is 3%, the oleamide content is 5%, N, N'-bis-(3-(3,5-di-ter...
PUM
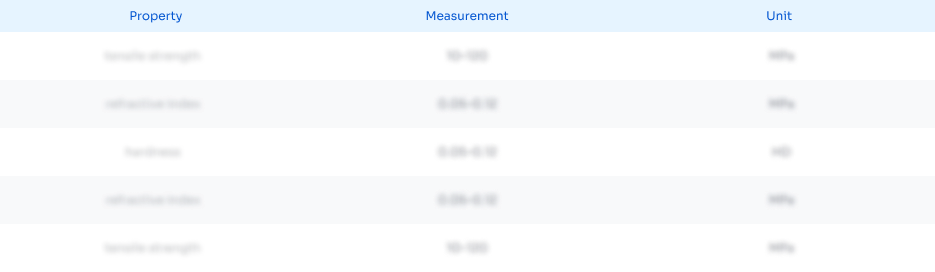
Abstract
Description
Claims
Application Information

- R&D
- Intellectual Property
- Life Sciences
- Materials
- Tech Scout
- Unparalleled Data Quality
- Higher Quality Content
- 60% Fewer Hallucinations
Browse by: Latest US Patents, China's latest patents, Technical Efficacy Thesaurus, Application Domain, Technology Topic, Popular Technical Reports.
© 2025 PatSnap. All rights reserved.Legal|Privacy policy|Modern Slavery Act Transparency Statement|Sitemap|About US| Contact US: help@patsnap.com