A finish-milling high-precision guide-surface welding type cemented carbide spiral end mill
A technology of cemented carbide and end mills, applied in the field of machining metal cutting
- Summary
- Abstract
- Description
- Claims
- Application Information
AI Technical Summary
Problems solved by technology
Method used
Image
Examples
Embodiment Construction
[0026] The present invention will be further described below in conjunction with the accompanying drawings.
[0027] like Figure 1-Figure 4 Shown, a kind of fine milling high-precision guide rail surface welding type cemented carbide spiral end mill, the fine milling guide rail surface cemented carbide spiral end mill of the present invention has a cutter body and several hard alloys welded on the cutter body Composed of alloy spiral blades, the cutter body is made of 9crsi alloy steel, and the blade material is YL10.2. The simple production process is: cutting, turning, milling, quenching HRC56-60, welding and grinding the center hole, external grinding, CNC five-axis linkage tool grinding, open side cutting edge and end face cutting edge and fine grinding of the tip arc.
[0028] In order to ensure that the reference runout of the side blade and the end face blade to the handle is less than 0.008mm, it is required that the precision of the chuck holding the handle of the C...
PUM
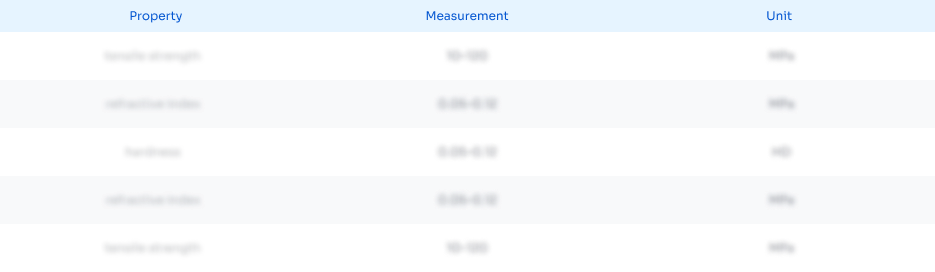
Abstract
Description
Claims
Application Information

- R&D
- Intellectual Property
- Life Sciences
- Materials
- Tech Scout
- Unparalleled Data Quality
- Higher Quality Content
- 60% Fewer Hallucinations
Browse by: Latest US Patents, China's latest patents, Technical Efficacy Thesaurus, Application Domain, Technology Topic, Popular Technical Reports.
© 2025 PatSnap. All rights reserved.Legal|Privacy policy|Modern Slavery Act Transparency Statement|Sitemap|About US| Contact US: help@patsnap.com