Method for preparing iron-based superconducting wire
An iron-based superconducting and wire technology, which is applied in cable/conductor manufacturing, electrical components, circuits, etc., can solve the problem of reducing the transmission performance of wires
- Summary
- Abstract
- Description
- Claims
- Application Information
AI Technical Summary
Problems solved by technology
Method used
Image
Examples
Embodiment 1
[0020] Put the powder of LaFeAsOF (La-1111) into the Nb tube, and the structure of the single-core iron-based strip after swaging, drawing and rolling is as follows Figure 3a As shown, after sealing the two ends of the above-mentioned strips separately, put them into high-temperature and high-pressure equipment, such as figure 1 shown. Pressurize to 10MPa at room temperature, then heat up to 500°C and keep warm for 20 hours, then cool down to room temperature, such as figure 2 shown. Take out the sample to make iron-based superconducting wire. During the high-pressure process, the pressure is always kept at 10MPa, and the high-pressure gas introduced into the high-pressure heat treatment process is argon.
Embodiment 2
[0022] Put the powder of LaFeAsOF (La-1111) into the Nb tube, and the structure of the single-core iron-based wire after swaging and drawing is as follows: Figure 3b As shown, after the two ends of the above-mentioned wires are sealed, they are put into high temperature and high pressure equipment. Pressurize to 10MPa at room temperature, then heat up to 500°C and keep warm for 20 hours, then cool down to room temperature, such as figure 2 shown. Take out the sample to make iron-based superconducting wire. During the high-pressure process, the total pressure is always maintained at 110MPa, and the high-pressure gas is argon.
Embodiment 3
[0024] Put the powder of LaFeAsOF (La-1111) into the Nb tube, and obtain a 7-core wire rod after swaging and drawing. After sealing the two ends of the wire rod, put it into a high-temperature and high-pressure equipment. First pressurize to 200MPa at room temperature, then raise the temperature to 600°C and keep it warm for 20 hours, then cool down to room temperature, take out the sample, and then make the iron-based superconducting wire. During the high-pressure process, the total pressure is always maintained at 200MPa, and the high-pressure gas is argon.
PUM
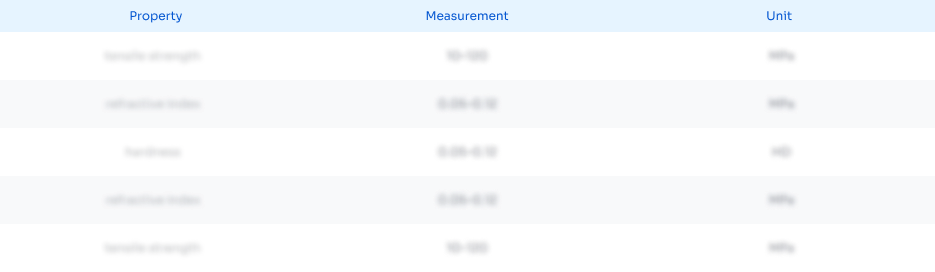
Abstract
Description
Claims
Application Information

- Generate Ideas
- Intellectual Property
- Life Sciences
- Materials
- Tech Scout
- Unparalleled Data Quality
- Higher Quality Content
- 60% Fewer Hallucinations
Browse by: Latest US Patents, China's latest patents, Technical Efficacy Thesaurus, Application Domain, Technology Topic, Popular Technical Reports.
© 2025 PatSnap. All rights reserved.Legal|Privacy policy|Modern Slavery Act Transparency Statement|Sitemap|About US| Contact US: help@patsnap.com