Main kiln pipe of rotary kiln
A rotary kiln and striker technology, applied in the field of rotary kiln, can solve the problems of fast heating speed, short holding time, and sticking of powder on the pipe wall, so as to reduce the heating and cooling speed, reduce the difficulty of cleaning the wall, and reduce the sticking of the wall Phenomenon-improving effect
- Summary
- Abstract
- Description
- Claims
- Application Information
AI Technical Summary
Problems solved by technology
Method used
Image
Examples
Embodiment Construction
[0017] The technical scheme of the present invention will be further described below in conjunction with the accompanying drawings and through specific embodiments:
[0018] The embodiment of the present invention provides a rotary kiln main kiln tube, such as figure 2 As shown, it includes: a kiln tube 21 made of stainless steel with a length greater than or equal to 11 meters; an insulating layer 22 set in the middle of the outside of the kiln tube 21; a first striker 23 and a second striker 24 located in the first group The front end of the heating group ( figure 2 Part A in the middle); the third striker 25, located at the rear end of the last group ( figure 2 Part B in the kiln), realize the design of 2 strikers in the kiln entry section of the raw material to be fired, and 1 striker in the kiln exit section, a total of 3 strikers. Of course, the number of strikers designed in the kiln entry section and the kiln exit section of the raw material to be fired can be adj...
PUM
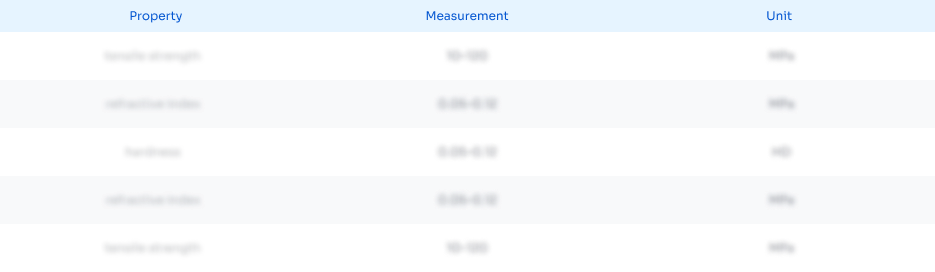
Abstract
Description
Claims
Application Information

- Generate Ideas
- Intellectual Property
- Life Sciences
- Materials
- Tech Scout
- Unparalleled Data Quality
- Higher Quality Content
- 60% Fewer Hallucinations
Browse by: Latest US Patents, China's latest patents, Technical Efficacy Thesaurus, Application Domain, Technology Topic, Popular Technical Reports.
© 2025 PatSnap. All rights reserved.Legal|Privacy policy|Modern Slavery Act Transparency Statement|Sitemap|About US| Contact US: help@patsnap.com