Energy-saving and environment-friendly cement clinker preparation system
A cement clinker and preparation system technology, applied in clinker production, cement production, etc., can solve problems that affect the stable operation of production, low powder selection efficiency, blockage of raw meal metering bin delivery pipelines, etc., and achieve saving equipment production and operation Cost, uniform and stable material feeding, and the effect of reducing the cycle load rate
- Summary
- Abstract
- Description
- Claims
- Application Information
AI Technical Summary
Problems solved by technology
Method used
Image
Examples
Embodiment 1
[0022] Embodiment 1: as figure 1 As shown, the energy-saving and environmentally friendly cement clinker preparation system includes a raw meal preparation system 1, a raw meal homogenization system 2, a kiln raw meal delivery system 3, a cement coal powder preparation system 4 and a cement clinker firing system 5;
[0023] Among them, such as figure 2As shown, the raw material preparation system 1 includes a mill-inlet bucket elevator 101, an adjustable ratio material distribution valve 102, two mill-inlet quantitative feeders 103, two raw material mills 104, a mill-out quantitative feeder 105, and an out-of-mill quantitative feeder 105. Mill screw conveyor 106, mill outlet air delivery chute 107, two powder flowmeters 108, PLC controller 109, mill outlet bucket elevator 110, powder selection air delivery chute 111, combined high-efficiency powder separator 112 , Air conveying chute 113 at the discharge port of powder separator, air conveying chute for raw material output 1...
PUM
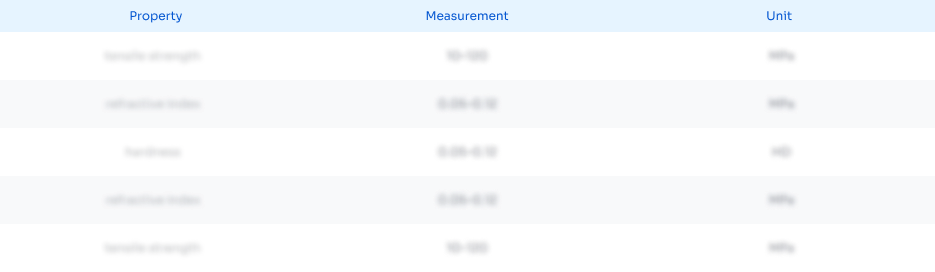
Abstract
Description
Claims
Application Information

- R&D
- Intellectual Property
- Life Sciences
- Materials
- Tech Scout
- Unparalleled Data Quality
- Higher Quality Content
- 60% Fewer Hallucinations
Browse by: Latest US Patents, China's latest patents, Technical Efficacy Thesaurus, Application Domain, Technology Topic, Popular Technical Reports.
© 2025 PatSnap. All rights reserved.Legal|Privacy policy|Modern Slavery Act Transparency Statement|Sitemap|About US| Contact US: help@patsnap.com