System and method for abating three-step frequency vibration of fan blades on IN-PLANE
A technology of fan impeller and rotating plane, which is applied in the control of wind turbines, wind turbines, machines/engines, etc. It can solve the problems of slow dynamic response speed, inability to reduce vibration, and poor dynamic characteristics, etc., and achieve overshoot Effects of reduced, shorter response time, increased bandwidth
- Summary
- Abstract
- Description
- Claims
- Application Information
AI Technical Summary
Problems solved by technology
Method used
Image
Examples
Embodiment Construction
[0027] Embodiments of the invention will now be described in detail, examples of which are illustrated in the accompanying drawings, wherein like reference numerals refer to like parts throughout. The embodiments are described below in order to explain the present invention by referring to the figures.
[0028] figure 1 It is a block diagram showing an IN-PLANE third-order frequency vibration suppression system for fan blades according to an embodiment of the present invention.
[0029] refer to figure 1 , the fan blade IN-PLANE third-order frequency vibration suppression system includes a generator speed measurement module (not shown), a comparator 101, a proportional-integral (PI) controller 102, a band-pass filter 103, a differential module 104, and a proportional gain module 105 and adder 106.
[0030] The generator speed measurement module is installed in the wind turbine nacelle, and measures the generator speed (ie, obtains the measured value of the generator speed)....
PUM
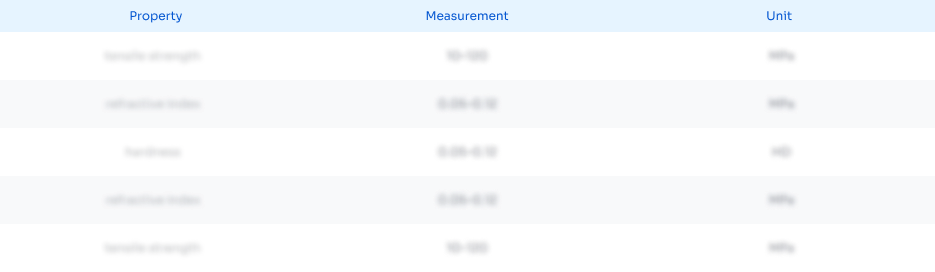
Abstract
Description
Claims
Application Information

- Generate Ideas
- Intellectual Property
- Life Sciences
- Materials
- Tech Scout
- Unparalleled Data Quality
- Higher Quality Content
- 60% Fewer Hallucinations
Browse by: Latest US Patents, China's latest patents, Technical Efficacy Thesaurus, Application Domain, Technology Topic, Popular Technical Reports.
© 2025 PatSnap. All rights reserved.Legal|Privacy policy|Modern Slavery Act Transparency Statement|Sitemap|About US| Contact US: help@patsnap.com