Method for gas-phase vanadium extraction by utilizing combustion of stone coals in cyclone furnace
A cyclone furnace and gas technology, applied in the chemical and chemical industry, can solve the problems of increasing the burden of subsequent dust removal equipment, fly ash entrainment, and short powder burning time, so as to maintain continuity and adequacy, and achieve good heat and mass transfer effects , the effect of long residence time
- Summary
- Abstract
- Description
- Claims
- Application Information
AI Technical Summary
Problems solved by technology
Method used
Examples
Embodiment Construction
[0027] In order to better illustrate the present invention, the following clearly and completely describes the technical solutions in the embodiments of the present invention.
[0028] The process steps of the invention include:
[0029] (1) Put V 2 o 5 Stone coal raw materials with a content of more than 0.5% are crushed into pellets with a particle size of <20mm, added with 5% anthracite, mixed and then ground into powders of 0.5-1.0mm;
[0030] (2) The powder and the air with an oxygen content of 21% to 30% enter the cyclone along the axial direction and tangential direction of the cylinder respectively, and the powder is thrown to the hot slag film on the inner wall of the cyclone, and the residence time is longer;
[0031] (3) Control the temperature in the furnace at 1300-1500°C, the carbon in the stone coal is almost burned out, and the low-priced vanadium is oxidized and gasified into gaseous vanadium pentoxide, which is discharged together with the furnace gas and a...
PUM
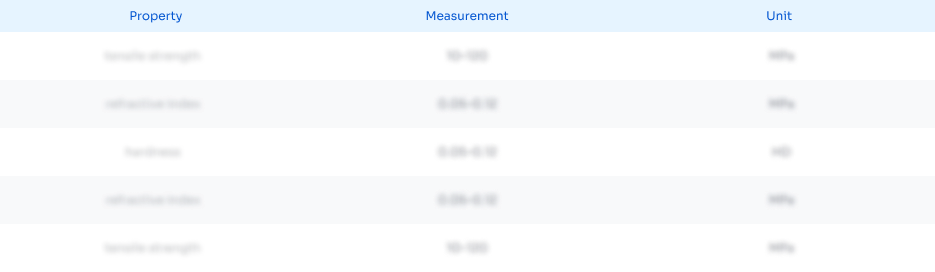
Abstract
Description
Claims
Application Information

- R&D
- Intellectual Property
- Life Sciences
- Materials
- Tech Scout
- Unparalleled Data Quality
- Higher Quality Content
- 60% Fewer Hallucinations
Browse by: Latest US Patents, China's latest patents, Technical Efficacy Thesaurus, Application Domain, Technology Topic, Popular Technical Reports.
© 2025 PatSnap. All rights reserved.Legal|Privacy policy|Modern Slavery Act Transparency Statement|Sitemap|About US| Contact US: help@patsnap.com