New process for producing low-alloy structural steel by adding ferro-vanadium-nitride
A ferrovanadium nitride and low-alloy technology, applied in the field of new production process of low-alloy structural steel, can solve the problems of reduced toughness, unqualified strength, banded structure, etc., and achieve the effect of reducing the amount of addition and reducing the cost per ton of steel
- Summary
- Abstract
- Description
- Claims
- Application Information
AI Technical Summary
Problems solved by technology
Method used
Image
Examples
Embodiment 1
[0015] (1) Converter smelting: The chemical composition is controlled as follows: C: 0.13%, Si: 0.12%, Mn: 0.75%, P: 0.019%, S: 0.007%, V: 0.028%, Fe balance;
[0016] (2) LF refining: before refining, the temperature is 1589℃, the free oxygen is 25ppm, and the thickness of the slag layer is 35mm; after refining, the oxygen content is 11ppm, R: 3.5, FeO: 0.6%; after refining, the calcium treatment is 2.7 m / ton of steel;
[0017] (3) Continuous casting: 150*770 section, pulling speed 1.05±0.05m / min;
[0018] (4) Hot rolling: the temperature in the soaking section of the heating furnace is 1260 °C, and the slab is cold loaded in the furnace for 100 minutes; the rough rolling temperature is 1190 °C, the finishing rolling temperature is 880 °C, and the coiling temperature is 660 °C. The cooling method adopts Front section cooling (only the first four groups of cooling water are turned on).
Embodiment 2
[0020] (1) Converter smelting: The chemical composition is controlled as follows: C: 0.15%, Si: 0.16%, Mn: 0.70%, P: 0.020%, S: 0.009%, V: 0.025%, Fe balance;
[0021] (2) LF refining: Before refining, the temperature is 1585℃, the free oxygen is 20ppm, and the thickness of the slag layer is 40mm; after refining, the oxygen content is 10ppm, R: 3.8, FeO: 0.7%; after refining, the calcium treatment is 2.9 m / ton of steel;
[0022] (3) Continuous casting: 150*770 section, pulling speed 1.05±0.05m / min;
[0023] (4) Hot rolling: the temperature in the soaking section of the heating furnace is 1270 °C, the slab is cold loaded in the furnace for 110 minutes, the rough rolling temperature is 1185 °C, the finishing rolling temperature is 872 °C, and the coiling temperature is 665 °C. The cooling method adopts Front section cooling (only the first four groups of cooling water are turned on).
Embodiment 3
[0025] (1) Converter smelting: The chemical composition is controlled as follows: C: 0.14%, Si: 0.15%, Mn: 0.68%, P: 0.018%, S: 0.008%, V: 0.026%, Fe balance;
[0026] (2) LF refining: Before refining, the temperature is 1583℃, the free oxygen is 27ppm, and the thickness of the slag layer is 41mm; after refining, the oxygen content is 16ppm, R: 4.1, FeO: 0.8%, and the calcium treatment after refining is 2.5 m / ton of steel;
[0027] (3) Continuous casting: section 150*810, pulling speed 1.00±0.05 m / min;
[0028] (4) Hot rolling: the temperature in the soaking section of the heating furnace is 1270 °C, and the slab is hot charged in the furnace for 90 minutes; the rough rolling temperature is 1183 °C, the finishing rolling temperature is 869 °C, and the coiling temperature is 668 °C. The cooling method adopts Front section cooling (only the first four groups of cooling water are turned on).
PUM
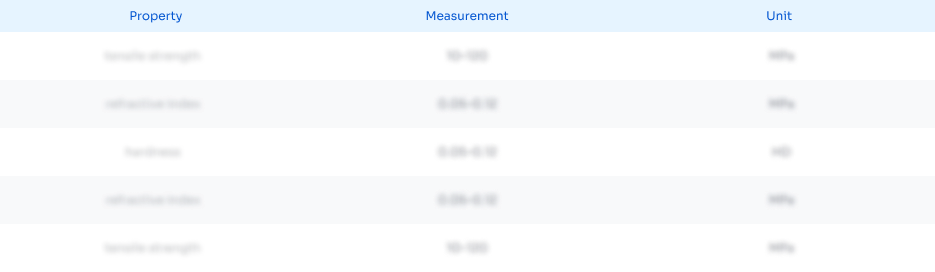
Abstract
Description
Claims
Application Information

- Generate Ideas
- Intellectual Property
- Life Sciences
- Materials
- Tech Scout
- Unparalleled Data Quality
- Higher Quality Content
- 60% Fewer Hallucinations
Browse by: Latest US Patents, China's latest patents, Technical Efficacy Thesaurus, Application Domain, Technology Topic, Popular Technical Reports.
© 2025 PatSnap. All rights reserved.Legal|Privacy policy|Modern Slavery Act Transparency Statement|Sitemap|About US| Contact US: help@patsnap.com