Grinding method of outer flange of third generation automobile hub ball bearing
An automobile wheel hub and outer flange technology, applied in grinding/polishing equipment, grinding machines, metal processing equipment, etc., can solve the problems of low processing efficiency, low qualification rate, affecting the reliability and safety of vehicles, etc. The effect of simplicity, low labor intensity and improved dimensional consistency
- Summary
- Abstract
- Description
- Claims
- Application Information
AI Technical Summary
Problems solved by technology
Method used
Image
Examples
Embodiment Construction
[0014] The specific embodiment of the present invention is described below in conjunction with accompanying drawing as follows: figure 1 As shown, the grinding steps of the third-generation automobile hub ball bearing outer flange grinding method described in the present invention are as follows:
[0015] 1. The large end face of the outer flange part 1 is used as the end face positioning reference, the outer circular surface of the front end of the outer flange part 1 is used as the radial positioning reference, and the electromagnetic centerless fixture 5 is used as the grinding positioning tool for the outer flange part 1;
[0016] 2. The workpiece feeding carriage is driven by the numerical control system to drive the ball screw system to realize the Z-axis workpiece feeding and trimming compensation movement. The speed of the forming grinding wheel 2 is high-speed at a speed of 10000 rpm, so that the profile of the profile grinding wheel 2 is conjugate to the profile of t...
PUM
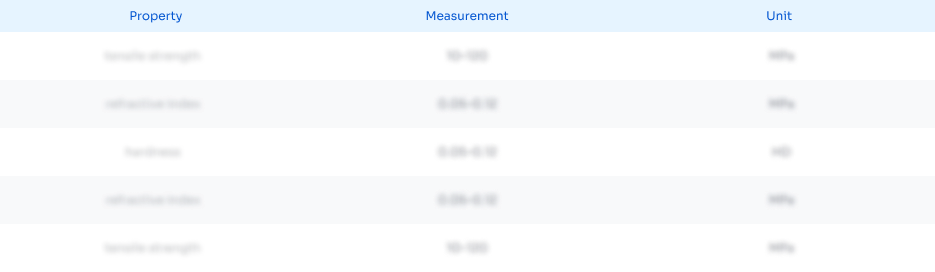
Abstract
Description
Claims
Application Information

- R&D
- Intellectual Property
- Life Sciences
- Materials
- Tech Scout
- Unparalleled Data Quality
- Higher Quality Content
- 60% Fewer Hallucinations
Browse by: Latest US Patents, China's latest patents, Technical Efficacy Thesaurus, Application Domain, Technology Topic, Popular Technical Reports.
© 2025 PatSnap. All rights reserved.Legal|Privacy policy|Modern Slavery Act Transparency Statement|Sitemap|About US| Contact US: help@patsnap.com