Preparation method of crosslinked polystyrene-immobilized benzothiazole catalyst used for formose reaction
A cross-linked polystyrene and benzothiazole technology, applied in chemical instruments and methods, physical/chemical process catalysts, organic compound/hydride/coordination complex catalysts, etc., can solve the problem of non-recyclable and mechanically difficult product separation , uneven mass transfer and other problems, to achieve the effect of easy recycling, easy operation of reaction, and uniform mass transfer
- Summary
- Abstract
- Description
- Claims
- Application Information
AI Technical Summary
Problems solved by technology
Method used
Image
Examples
Embodiment 1
[0031] (1) Preparation of BE-PS:
[0032] Weigh 7g (66.6mmol) of cross-linked polystyrene (cross-linking degree 4%) after long-term low-temperature drying (drying temperature 60°C, drying time 10h), add it to 40ml 1,2-dichloroethane In the three-necked flask, swell at room temperature for 2h, then add 4g of anhydrous AlCl to the three-necked flask 3 , and slowly add 60g of 1,2-dibromoethane dropwise, and stir the reaction at 50°C for 20h, then stop the reaction, cool to room temperature, and then use ethanol, CCl 4 , washed with distilled water, and then dried at 60°C for 10 hours to obtain bromoethylated cross-linked polystyrene (BE-PS). The content of bromine atoms measured by the Volhard method is 17.65% (mass fraction), 2.21mmol / g (the number of moles of bromine atoms per gram of BE-PS).
[0033] (2) Preparation of BETZB-PS:
[0034] Weigh 7g of BE-PS, add it to a three-necked flask containing 30ml of 1,2-dichloroethane, add 10g of benzothiazole, reflux for 24 hours, co...
Embodiment 2
[0038] (1) Preparation of BE-PS:
[0039] Weigh 7g (66.6mmol) of cross-linked polystyrene (cross-linking degree: 2.5%) after long-term low-temperature drying (drying temperature 60°C, drying time 10h), add to 40ml 1,2-dichloroethane In a three-necked flask, swell at room temperature for 2h, and then add 2g of anhydrous AlCl to the three-necked flask 3 , and slowly dropwise added 40g of 1,2-dibromoethane, stirred at 50°C for 15h, stopped the reaction, cooled to room temperature, followed by ethanol, CCl 4 , washed with distilled water, and then dried at 60°C for 10 hours to obtain bromoethylated cross-linked polystyrene (BE-PS). The content of bromine atoms measured by the Volhard method was 11.08% (mass fraction), 1.39mmol / g.
[0040] (2) Preparation of BETZB-PS:
[0041] Weigh 7g of BE-PS, add it into a three-necked flask containing 40ml of 1,2-dichloroethane, add 10g of benzothiazole, reflux for 40h, cool to room temperature after the reaction, and use 1,2-dichloroethane ...
Embodiment 3
[0043] (1) Preparation of BE-PS:
[0044] Weigh 7g (66.6mmol) of cross-linked polystyrene (cross-linking degree: 7%) after long-term low-temperature drying (drying temperature 60°C, drying time 10h), add to 40ml 1,2-dichloroethane In the three-necked flask, swell at room temperature for 2h, then add 4g of anhydrous AlCl to the three-necked flask 3 , and slowly add 40g of 1,2-dibromoethane dropwise, and stir the reaction at 40°C for 20h, then stop the reaction, cool to room temperature, and then use ethanol, CCl 4, washed with distilled water, and then dried at 60°C for 10 hours to obtain bromoethylated cross-linked polystyrene (BE-PS). The content of bromine atoms measured by the Volhard method is 13.93% (mass fraction), 1.74mmol / g (the number of moles of bromine atoms per gram of BE-PS).
[0045] (2) Preparation of BETZB-PS:
[0046] Weigh 7g of BE-PS, add it to a three-necked flask containing 40ml of 1,2-dichloroethane, add 5g of benzothiazole, reflux for 15h, cool to roo...
PUM
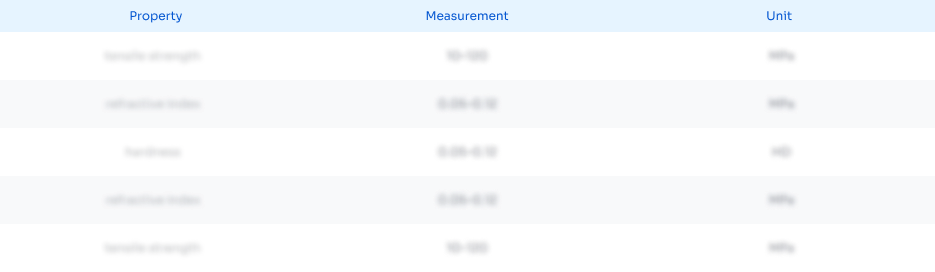
Abstract
Description
Claims
Application Information

- R&D Engineer
- R&D Manager
- IP Professional
- Industry Leading Data Capabilities
- Powerful AI technology
- Patent DNA Extraction
Browse by: Latest US Patents, China's latest patents, Technical Efficacy Thesaurus, Application Domain, Technology Topic, Popular Technical Reports.
© 2024 PatSnap. All rights reserved.Legal|Privacy policy|Modern Slavery Act Transparency Statement|Sitemap|About US| Contact US: help@patsnap.com