Process for manufacturing lower chlorides of titanium
A preparation process, low-valent titanium chloride technology, applied in the direction of titanium trichloride, titanium halide, process efficiency improvement, etc., can solve the problems of expensive process, unmentioned reagent recovery and recycling, complex and other problems
- Summary
- Abstract
- Description
- Claims
- Application Information
AI Technical Summary
Problems solved by technology
Method used
Examples
Embodiment 1
[0067] Weigh 700 g of equimolar NaCl and KCl (308 parts of NaCl and 392 parts of KCl) into a clay-graphite reactor. The mixed salts are refined and dried by heating and passing through dry HCl. Finally, the reactor was purged of air with inert argon. The reactor was heated in an electric furnace, and the temperature was slowly raised to 750° C. under an argon atmosphere. About 1400g of titanium tetrachloride liquid is passed into a steel evaporator at a rate of 200g / h. Reducing gas H from cylinder 2 , bubbled through a titanium tetrachloride evaporator. TiCl 4 Steam and H 2 The mixture passes through a ceramic sparger and is bubbled in a molten salt bath. During reduction, TiCl 4 with H 2 The molar ratio was maintained at 1:1. Reduced TiCl 4 , to obtain TiCl in situ 3 , And with alkali metal chlorides, generate chlorine complexes. Condensation of unreacted TiCl 4 , Wash the by-product HCl with dilute lye. According to the change of normal concentration of lye, ca...
Embodiment 2
[0069] Place a graphite crucible in a steel reactor, and prepare 10kg of mixed salt, which contains 32mol% NaCl, 48mol% KCl and 20mol% CaCl 2 . The mixed salt was refined and degassed as described in Example 1. The mixed salts were melted under an inert atmosphere, and the melt temperature was maintained at 700 °C. In molten liquid, with TiCl 4 and H 2 The vapor mixture is bubbling. During reduction, by controlling the TiCl 4 Evaporation and H 2 gas flow rate, maintain TiCl 4 with H 2 The stoichiometric ratio is 1:4. The bubbling and dispersion of the vapor mixture is carried out by placing multiple ceramic dip tubes into the molten bath. Analysis of TiCl 3 content, it was found that the content was 30%, and the efficiency was 96.5%.
Embodiment 3
[0071] In a reduction reactor whose outer layer is clay graphite and inner brick lining, by adding 25mol% CaCl 2 And 75mol% KCl, the preparation of molten bath. The mixed salt (120 kg) was dried and melted with the help of a graphite resistance heater provided at the bottom of the reactor. Seal the reactor with a high temperature rope gasket to prevent gas leakage. During the reduction, the reactor temperature was maintained at 700°C. Through multiple clay-graphite dip tubes, adding TiCl 4 and H 2 Vapor to generate agitation and dispersion in the molten bath. Pass 4500g / h TiCl 4 , with a 1:4 molar ratio of reduced H 2 Together, restore. Unreacted TiCl 4 Condensates in multiple condensers and circulates back to the evaporator. Likewise, excess hydrogen passes through a series of HCl scrubbers and dehydration towers (with a concentrated sulfuric acid cycle) and is recycled back into the reaction system. TiCl 4 to TiCl 3 The conversion rate was confirmed to be 97%.
PUM
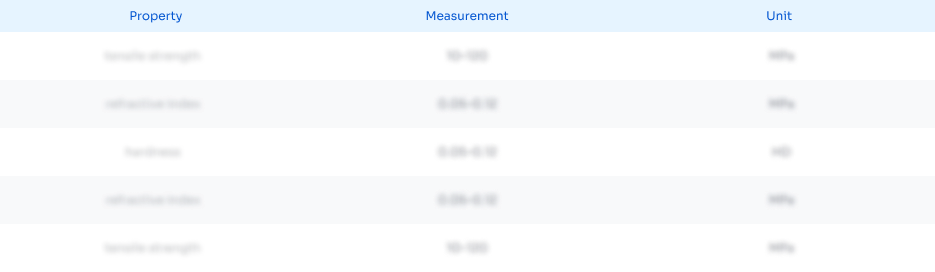
Abstract
Description
Claims
Application Information

- R&D
- Intellectual Property
- Life Sciences
- Materials
- Tech Scout
- Unparalleled Data Quality
- Higher Quality Content
- 60% Fewer Hallucinations
Browse by: Latest US Patents, China's latest patents, Technical Efficacy Thesaurus, Application Domain, Technology Topic, Popular Technical Reports.
© 2025 PatSnap. All rights reserved.Legal|Privacy policy|Modern Slavery Act Transparency Statement|Sitemap|About US| Contact US: help@patsnap.com