Preparation of crude titanic chloride
A technology of crude titanium tetrachloride and boiling chlorination, applied in the direction of titanium halide, etc., can solve the problems of TiO2 content not more than 90%, consumption and the like
- Summary
- Abstract
- Description
- Claims
- Application Information
AI Technical Summary
Problems solved by technology
Method used
Image
Examples
Embodiment Construction
[0020] Embodiments of the invention: at first, TiO in natural rutile 2 The content is basically 96%, and the carbon content in metallurgical coke is basically 91.8%. The weight ratio of natural rutile to metallurgical coke is: 100:22.74. Since the price of natural rutile is higher, and metallurgical coke is cheaper, it can be considered to increase appropriately The amount of metallurgical coke is subjected to boiling chlorination. Before chlorination, metallurgical coke must be dried by hot air flow and then pulverized.
[0021] The production capacity of this system is 195,000 tons / year of crude titanium tetrachloride. In this way, when the natural rutile added to the chlorination furnace is 11476.08kg per hour, it is necessary to chlorinate with chlorine gas in the boiling chlorination stage, and the chlorine gas per hour is chlorinated. The amount of chlorine gas required for chemical purification is 20.848 tons.
[0022] After the boiling chlorination stage, the air volu...
PUM
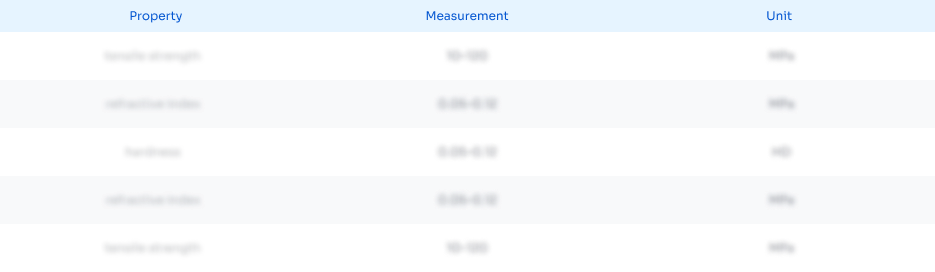
Abstract
Description
Claims
Application Information

- Generate Ideas
- Intellectual Property
- Life Sciences
- Materials
- Tech Scout
- Unparalleled Data Quality
- Higher Quality Content
- 60% Fewer Hallucinations
Browse by: Latest US Patents, China's latest patents, Technical Efficacy Thesaurus, Application Domain, Technology Topic, Popular Technical Reports.
© 2025 PatSnap. All rights reserved.Legal|Privacy policy|Modern Slavery Act Transparency Statement|Sitemap|About US| Contact US: help@patsnap.com