Enamel treatment technology for internal wall of steel radiator
A treatment process and radiator technology, applied in coatings and other directions, can solve the problems of poor quality of internal anti-corrosion coatings and shortened service life, and achieve the effect of solving corrosion leakage, low cost and reducing replacement budget funds.
- Summary
- Abstract
- Description
- Claims
- Application Information
AI Technical Summary
Problems solved by technology
Method used
Examples
Embodiment 1
[0023] Immerse the single piece or group of steel radiators in hydrochloric acid solution with a mass concentration of 1% to remove oil and rust on the inner and outer surfaces of the single piece or group of steel radiators. The immersion time depends on the temperature of the single piece or group of radiators Depending on the degree of oil pollution and floating rust pollution;
[0024] Immerse the single piece or group of steel radiators after pickling in a sodium hydroxide solution with a mass concentration of 2% to neutralize the residual hydrochloric acid solution during the pickling process;
[0025] Immerse the single piece or group of steel radiators after alkali washing in water and wash them, dilute and remove the residual liquid after neutralization after pickling and alkali washing;
[0026] Immerse the washed steel radiator sheet or group sheet in the phosphating solution with a mass concentration of 5% to form a protective film;
[0027] Fill the above-mention...
Embodiment 2
[0031] Immerse the single piece or group of steel radiators in a hydrochloric acid solution with a mass concentration of 3%, and remove the oil and rust on the inner and outer surfaces of the single piece or group of steel radiators;
[0032] Immerse the pickled steel radiator single sheet or group sheet in a sodium hydroxide solution with a mass concentration of 4%;
[0033] Submerge the single piece or group of steel radiators after alkali cleaning in water for washing;
[0034] Immerse the washed steel radiator sheet or group sheet in the phosphating solution with a mass concentration of 8%;
[0035] Fill the above-mentioned steel radiator single piece or group piece with enamel powder slurry;
[0036] 50°C hot air circulation to dry and cure the inner coating;
[0037] Bake the inner coating at 800°C for 4 minutes.
Embodiment 3
[0039] Immerse the single piece or group of steel radiators in a hydrochloric acid solution with a mass concentration of 3%, and remove the oil and rust on the inner and outer surfaces of the single piece or group of steel radiators;
[0040] Immerse the pickled steel radiator single sheet or group sheet in a sodium hydroxide solution with a mass concentration of 5%;
[0041] Submerge the single piece or group of steel radiators after alkali cleaning in water for washing;
[0042] Immerse the washed steel radiator sheet or group sheet in the phosphating solution with a mass concentration of 10%;
[0043] Fill the above-mentioned steel radiator single piece or group piece with enamel powder slurry;
[0044] 60 ℃ hot air circulation to dry and cure the inner coating;
[0045] Bake the inner coating at 860°C for 5 minutes.
PUM
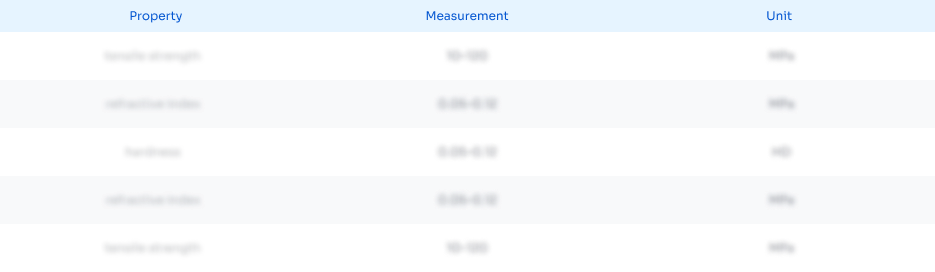
Abstract
Description
Claims
Application Information

- Generate Ideas
- Intellectual Property
- Life Sciences
- Materials
- Tech Scout
- Unparalleled Data Quality
- Higher Quality Content
- 60% Fewer Hallucinations
Browse by: Latest US Patents, China's latest patents, Technical Efficacy Thesaurus, Application Domain, Technology Topic, Popular Technical Reports.
© 2025 PatSnap. All rights reserved.Legal|Privacy policy|Modern Slavery Act Transparency Statement|Sitemap|About US| Contact US: help@patsnap.com