Method for preparing zirconium oxide thermal barrier coating by spraying process
A thermal barrier coating, zirconia technology, applied in the field of material science, can solve problems such as coating failure, and achieve the effects of less agglomeration, high reactivity, and excellent resistance to molten salt corrosion.
- Summary
- Abstract
- Description
- Claims
- Application Information
AI Technical Summary
Problems solved by technology
Method used
Examples
Embodiment 1
[0043] A, the preparation of nanoscale ZrO2 powder
[0044] (1) Weigh 230 parts by weight of Zr(OH) 4 and 33 parts by weight of YCl 3 , added to deionized water to prepare an acidic solution with a concentration of 6%, heated to 65°C under stirring conditions, completely dissolved and mixed thoroughly;
[0045] (2) Take 660 parts by weight of potassium hydroxide, add it to deionized water to prepare a 13% alkaline solution, add the acidic solution prepared in the above steps dropwise to the alkaline solution at a constant speed, and adjust the pH value to 9.4, so that Co-precipitate the two salts to obtain yttria-stabilized zirconia with crystal water, and precipitate for 3 hours to obtain a hydrogel;
[0046] (3) Add a dispersant and an alkali-removing agent to the hydrogel prepared in the above steps, beat and filter, and the Zr(OH) after washing with deionized water 4 AgNO for hydrogel 3 Check until no Cl is detected - ; The dispersant adopts PEG4000, and the addition ...
Embodiment 2
[0055] A, the preparation of nanoscale ZrO2 powder
[0056] (1) Weigh 240 parts by weight of Zr(OH) 4 and 29 parts by weight of YCl 3 , added to deionized water to prepare an acidic solution with a concentration of 6%, heated to 65°C under stirring conditions, completely dissolved and mixed thoroughly;
[0057](2) Take 680 parts by weight of potassium hydroxide, add it into deionized water to prepare a 13% alkaline solution, add the acidic solution prepared in the above steps into the alkaline solution dropwise at a uniform speed, and adjust the pH value to 9.3, so that Co-precipitate the two salts to obtain yttria-stabilized zirconia with crystal water, and precipitate for 3 hours to obtain a hydrogel;
[0058] (3) Add a dispersant and an alkali-removing agent to the hydrogel prepared in the above steps, beat and filter, and the Zr(OH) after washing with deionized water 4 AgNO for hydrogel 3 Check until no Cl is detected - ; The dispersant adopts PEG4000, and the additio...
Embodiment 3
[0067] A, the preparation of nanoscale ZrO2 powder
[0068] (1) Weigh 250 parts by weight of Zr(OH) 4 and 27 parts by weight of YCl 3 , added to deionized water to prepare an acidic solution with a concentration of 6%, heated to 65°C under stirring conditions, completely dissolved and mixed thoroughly;
[0069] (2) Take 690 parts by weight of potassium hydroxide, add it to deionized water to prepare a 13% alkaline solution, add the acidic solution prepared in the above steps dropwise to the alkaline solution at a constant speed, and adjust the pH value to 9.5, so that Co-precipitate the two salts to obtain yttria-stabilized zirconia with crystal water, and precipitate for 3 hours to obtain a hydrogel;
[0070] (3) Add a dispersant and an alkali-removing agent to the hydrogel prepared in the above steps, beat and filter, and the Zr(OH) after washing with deionized water 4 AgNO for hydrogel 3 Check until no Cl is detected - ; The dispersant adopts PEG4000, and the addition ...
PUM
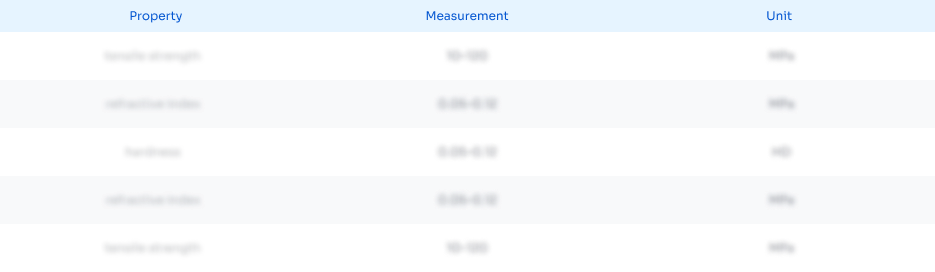
Abstract
Description
Claims
Application Information

- R&D
- Intellectual Property
- Life Sciences
- Materials
- Tech Scout
- Unparalleled Data Quality
- Higher Quality Content
- 60% Fewer Hallucinations
Browse by: Latest US Patents, China's latest patents, Technical Efficacy Thesaurus, Application Domain, Technology Topic, Popular Technical Reports.
© 2025 PatSnap. All rights reserved.Legal|Privacy policy|Modern Slavery Act Transparency Statement|Sitemap|About US| Contact US: help@patsnap.com