Transparent sound-absorption film surface hydrophobic self-cleaning coating and preparation method thereof
A sound-absorbing and thin-film technology, applied in the direction of coating, etc., can solve problems such as expensive raw materials, micropore blockage on the surface of sound-absorbing film, corrosion of sound-absorbing materials, etc., to achieve expanded use environment, good hydrophobic effect, and low manufacturing cost Effect
- Summary
- Abstract
- Description
- Claims
- Application Information
AI Technical Summary
Problems solved by technology
Method used
Image
Examples
preparation example Construction
[0029] A method for preparing a hydrophobic self-cleaning coating on the surface of a transparent sound-absorbing film of the present invention comprises the following steps:
[0030] (1) Preparation of nano-silica particles; dissolve tetraethyl orthosilicate in ethanol solution, stir to keep the temperature at 30~70°C, add ammonia solution and KH-570, tetraethyl orthosilicate to the mixture dropwise , The molar concentration ratio of ammonia water and KH-570 is 1:3.2:1.53~1:11.2:1.53, continue to react, after the reaction is completed, the mixed solution is dried and ground to obtain nano-silica particles;
[0031] (2) Preparation of polyvinylidene fluoride (PDVF) mixed solution: mix N-N-dimethylformamide and methyl ethyl ketone, add polyvinylidene fluoride powder to the mixture, N-N-dimethylformamide and butyl The ketone molar volume ratio is 4:1, the addition amount of polyvinylidene fluoride is 0.05g / ml, stir and dissolve to obtain a PDVF mixed solution;
[0032] (3) Prep...
Embodiment 1
[0036] (1) Dissolve tetraethyl orthosilicate (2ml) in (55mL) ethanol solution, stir to keep the temperature at 30°C, add ammonia solution and KH-570, tetraethyl orthosilicate, ammonia water and KH to the mixture dropwise The molar concentration ratio of -570 is 1:8:1.53, and the reaction is continued. After the reaction is completed, the mixed solution is dried and ground to obtain nano-silica particles;
[0037] (2) Preparation of polyvinylidene fluoride (PDVF) mixed solution: Mix 20mL N,N-dimethylformamide and 5mL butanone, add 1.25g polyvinylidene fluoride powder to the mixture, stir and dissolve to obtain PDVF mixture;
[0038] (3) Add the nano-silica particles prepared in step (1) to the PDVF mixed solution in step (2), and the amount of nano-silica particles added is 0.032 g / mL of the PDVF mixed solution. The mixed solution is centrifugally emulsified and ultrasonicated, and the ultrasonically dispersed solution is heated and stirred in a magnetic heating stirrer to mak...
Embodiment 2
[0042] (1) Dissolve tetraethyl orthosilicate (2ml) in (55mL) ethanol solution, stir to keep the temperature at 60°C, add ammonia solution and KH-570, tetraethyl orthosilicate, ammonia water and KH to the mixture dropwise The molar concentration ratio of -570 is 1:3.2:1.53, and the reaction is continued. After the reaction is completed, the mixed solution is dried and ground to obtain nano-silica particles;
[0043] (2) Preparation of polyvinylidene fluoride (PDVF) mixed solution: Mix 20mL N,N-dimethylformamide and 5mL butanone, add 1.25g polyvinylidene fluoride powder to the mixture, stir and dissolve to obtain PDVF mixture;
[0044] (3) Add the nano-silica particles prepared in step (1) to the PDVF mixed solution in step (2). The amount of nano-silica particles added is 0.024 g / mL of the PDVF mixed solution. The mixed solution is centrifugally emulsified and ultrasonicated, and the ultrasonically dispersed solution is heated and stirred in a magnetic heating stirrer to make ...
PUM
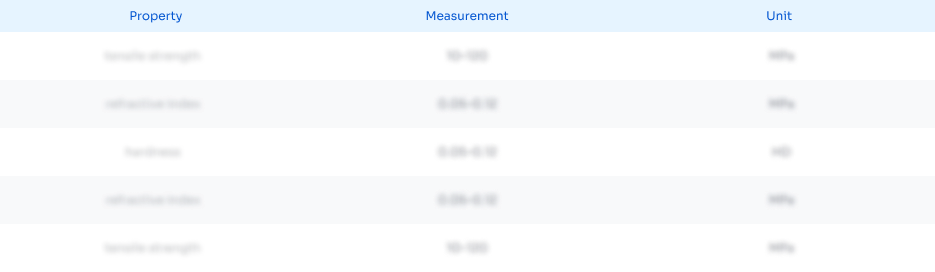
Abstract
Description
Claims
Application Information

- R&D
- Intellectual Property
- Life Sciences
- Materials
- Tech Scout
- Unparalleled Data Quality
- Higher Quality Content
- 60% Fewer Hallucinations
Browse by: Latest US Patents, China's latest patents, Technical Efficacy Thesaurus, Application Domain, Technology Topic, Popular Technical Reports.
© 2025 PatSnap. All rights reserved.Legal|Privacy policy|Modern Slavery Act Transparency Statement|Sitemap|About US| Contact US: help@patsnap.com