Starch full-biodegradable resin and continuous preparation method thereof
A technology of biodegradable resin and degradable resin, applied in the direction of fermentation, etc., can solve the problems of product mechanical properties and secondary processing performance decline, long dehydration cycle, high energy consumption, etc., to avoid mechanical properties and secondary processing performance decline, mechanical Excellent performance and secondary processing performance, excellent mechanical properties
- Summary
- Abstract
- Description
- Claims
- Application Information
AI Technical Summary
Problems solved by technology
Method used
Image
Examples
preparation example Construction
[0043] see figure 1, the present invention also provides a continuous preparation method of starch full biodegradable resin, comprising the steps of:
[0044] Step 1, adjust starch and water into starch milk according to the ratio of 1:3, heat to 55-75°C, stir to completely gelatinize the starch, and obtain uniform starch milk.
[0045] The starch can be one of corn starch, tapioca starch, potato starch, and mung bean starch. Different types of starch need to be heated to different temperatures, which can be selected according to actual conditions.
[0046] Step 2, adding a composite catalyst into the starch emulsion, and after fully reacting, carry out centrifugal dehydration separation, drying, and crushing to obtain high amylose with an amylose content of 50-70%, wherein the high amylose water content is 12-15% % parts by weight.
[0047] The composite catalyst is one or a combination of α-amylase, β-amylase, pullulanase, and isoamylase, and its addition ratio is 0.15-0.5...
Embodiment 1
[0075]Example 1: Take 20kg of tapioca starch and put it into the reaction kettle. After stirring, slowly put in a certain amount of deionized water and adjust it into starch milk, heat it to 65°C, stir to make the starch completely gelatinized, and then add 0.10kg of α-starch Enzyme, sterilized after reacting for a certain period of time, separated by centrifugation and dehydration, air-dried to obtain 50% high straight-chain cassava starch, mixed with 0.02kg dibutyltin dilaurate, 0.02kg lauroyl peroxide, and 1kg methyl methacrylate monomer Put it into the feeder, melt and graft in the twin-screw extruder to obtain the ST-g-MMA graft copolymer, after the reaction, the moisture, ungrafted monomer and The small molecules are extracted, the vacuum degree is 0.1MPa, and then 34.5kg of PBAT is fed through the side feeding device, and the extrusion air-cooled strands are cut into pellets to obtain about 52kg of starch biodegradable resin. Put this material into the blown film machin...
Embodiment 2
[0076] Example 2: Take 40kg of cornstarch and put it into the reactor, after stirring, slowly pour in a certain amount of deionized water and adjust it into starch milk, heat it to 70°C, stir to make the starch completely gelatinized, and then add 0.16kg of Purus Lanzyme, sterilized after reacting for a certain period of time, separated by centrifugal dehydration, and air-dried to obtain 55% high-amylose corn starch, together with 0.032kg dibutyltin dilaurate and 0.056kgH 2 o 2 / FeSO 4 , 2kg of lactide monomer is mixed evenly and put into the feeder, melted and grafted in the twin-screw extruder to obtain the ST-g-PLA graft copolymer, after the reaction, it is passed through the alternating condensation high vacuum anti-refilling method The device controls the vacuum degree of about 0.15MPa to extract water, ungrafted monomers and small molecules, and then puts 5.4kgPBS and 37.6kgPLA into the side feeding device, and carries out extrusion air-cooled strand cutting to obtain a...
PUM
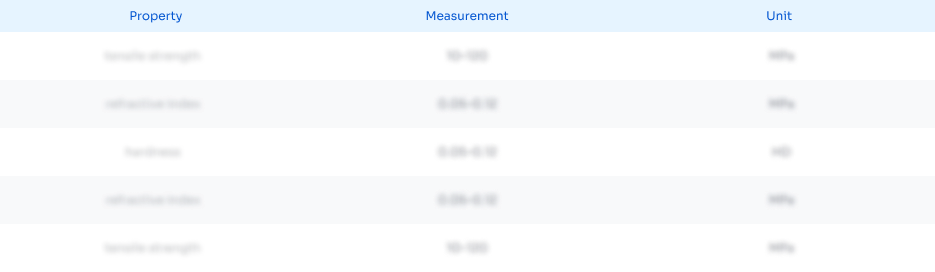
Abstract
Description
Claims
Application Information

- R&D
- Intellectual Property
- Life Sciences
- Materials
- Tech Scout
- Unparalleled Data Quality
- Higher Quality Content
- 60% Fewer Hallucinations
Browse by: Latest US Patents, China's latest patents, Technical Efficacy Thesaurus, Application Domain, Technology Topic, Popular Technical Reports.
© 2025 PatSnap. All rights reserved.Legal|Privacy policy|Modern Slavery Act Transparency Statement|Sitemap|About US| Contact US: help@patsnap.com