Continuous preparation process for environment-friendly plasticizer and device used in process
A preparation process and technology of plasticizers, applied in the field of plasticizers, can solve the problems of long time consuming and high energy consumption in the synthesis process
- Summary
- Abstract
- Description
- Claims
- Application Information
AI Technical Summary
Problems solved by technology
Method used
Image
Examples
Embodiment 1
[0028] Raw materials: terephthalic acid, isooctyl alcohol, tetrabutyl titanate;
[0029] After refining the isooctyl alcohol and terephthalic acid with a molar ratio of 2.2:1 to reach a particle size of 10 microns, pour into the raw material tank and start stirring to prevent sedimentation, fill the reaction tank with a feed pump, and add 1% ester catalyst For tetrabutyl titanate, turn on the condensed water, raise the temperature and turn on the circulating pump to make the material circulate and react, keep the pressure at 0.3MPa to 230°C to release the pressure; when there is a fraction distilled out, after the water is automatically separated, turn on the reflux pump and the preheater to reflux The isooctyl alcohol reaches 190°C and is re-injected into the reactor from the bottom of the reactor; when the acid value of the material in the reactor drops to 2mgKOH / g, the feed pump and outlet can be turned on to realize continuous reaction.
Embodiment 2
[0031] Raw materials: terephthalic acid, isooctyl alcohol, isopropyl titanate, sodium hypophosphite;
[0032] Refining isooctyl alcohol and terephthalic acid with a molar ratio of 2.4:1 are injected into the raw material tank and started to stir to prevent sedimentation. Fill the reactor with a feed pump and add 0.5% catalyst isopropyl titanate and antioxidant Sodium hypophosphite, turn on the condensate, heat up and turn on the circulation pump to make the material circulate and react, keep the pressure at 0.2MPa to 230°C, release the pressure and gradually vacuum to -0.005MPa; when there is a distillate, automatically divide the water, turn on the return pump And the preheater will reflow the isooctyl alcohol to 180°C and re-inject the reaction kettle from the bottom of the kettle; when the acid value of the material in the kettle drops to 2mgKOH / g, the feed pump and outlet can be turned on to realize continuous reaction.
Embodiment 3
[0034] Raw materials: terephthalic acid, isooctyl alcohol, tetrabutyl titanate, isopropyl titanate;
[0035] Refining isooctyl alcohol and terephthalic acid with a molar ratio of 2.1:1 are poured into the raw material tank and started to stir to prevent sedimentation, fill the reactor with a feed pump, and add a total of 1% catalyst tetrabutyl titanate and isopropyl titanate, turn on the condensate, heat up and turn on the circulation pump to circulate the material; when there is a fraction distilled out, the water will be separated automatically, turn on the reflux pump and preheater to bring the refluxed isooctyl alcohol to 220°C from the The bottom of the kettle is injected into the reaction kettle; when the acid value of the material in the kettle drops to 1mgKOH / g, the feed pump and outlet can be turned on to realize continuous reaction.
PUM
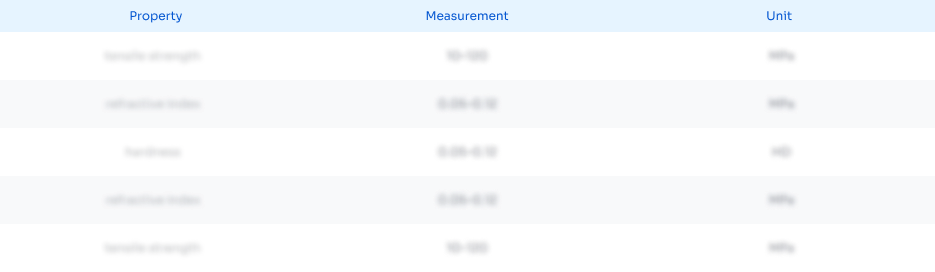
Abstract
Description
Claims
Application Information

- R&D
- Intellectual Property
- Life Sciences
- Materials
- Tech Scout
- Unparalleled Data Quality
- Higher Quality Content
- 60% Fewer Hallucinations
Browse by: Latest US Patents, China's latest patents, Technical Efficacy Thesaurus, Application Domain, Technology Topic, Popular Technical Reports.
© 2025 PatSnap. All rights reserved.Legal|Privacy policy|Modern Slavery Act Transparency Statement|Sitemap|About US| Contact US: help@patsnap.com