Heat treatment technology of iron casting for compressors
A technology for iron castings and compressors, which is applied in the field of heat treatment of iron castings for compressors, can solve the problems of low strength, impact toughness, corrosion resistance and wear resistance, uneven structure, and low production capacity of iron castings, and achieves The effect of shortening heat treatment time, improving comprehensive properties, and removing residual stress
- Summary
- Abstract
- Description
- Claims
- Application Information
AI Technical Summary
Problems solved by technology
Method used
Examples
Embodiment 1
[0014] A heat treatment process for iron castings for compressors, including low-temperature annealing, quenching and high-temperature tempering. The low-temperature annealing process is: heating up to 600°C at a heating rate of 45°C / hour, keeping the temperature for 4 hours, and then heating at 55°C / hour The cooling rate of 1 hour is air-cooled to below 160°C; the quenching process is: heating up to 930°C at a heating rate of 75°C / hour for 5 hours, and then cooling to below 160°C with the furnace; the tempering process is: The heating rate of °C / hour is to raise the temperature to 470 °C for 3 hours, and then cool down to below 160 °C with the furnace.
Embodiment 2
[0016] A heat treatment process for iron castings for compressors, including low-temperature annealing, quenching and high-temperature tempering. The low-temperature annealing process is: heating up to 610°C at a heating rate of 40°C / hour, holding the temperature for 4 hours, and then heating at 50°C / hour The cooling rate of 1 hour is air-cooled to below 160°C; the quenching process is: heating up to 920°C at a heating rate of 80°C / hour for 5 hours, and then cooling to below 160°C with the furnace; the tempering process is: The heating rate of °C / hour is to raise the temperature to 490 °C for 3 hours, and then cool down to below 160 °C with the furnace.
[0017] The heat treatment process of the iron castings for compressors of the present invention can shorten the heat treatment time by more than 50%. At the same time, the strength of the iron castings produced can be increased by about 15%, the impact toughness can be increased by more than 5%, and the energy consumption can ...
PUM
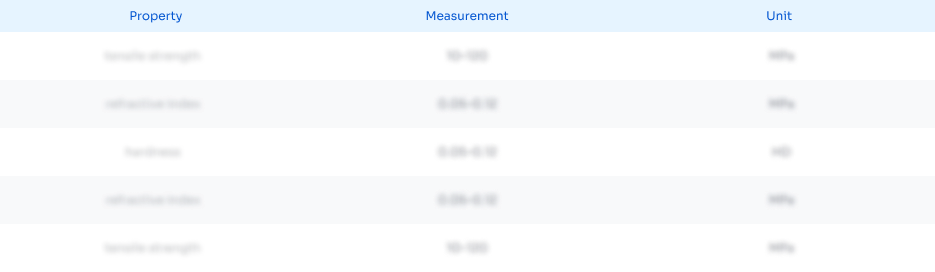
Abstract
Description
Claims
Application Information

- R&D Engineer
- R&D Manager
- IP Professional
- Industry Leading Data Capabilities
- Powerful AI technology
- Patent DNA Extraction
Browse by: Latest US Patents, China's latest patents, Technical Efficacy Thesaurus, Application Domain, Technology Topic, Popular Technical Reports.
© 2024 PatSnap. All rights reserved.Legal|Privacy policy|Modern Slavery Act Transparency Statement|Sitemap|About US| Contact US: help@patsnap.com