Gear tooth bottom forming milling cutter
A technology for forming milling cutters and gear teeth, which is applied in the direction of gear teeth, gear tooth manufacturing tools, gear tooth manufacturing devices, etc., can solve the problems that gear processing cannot reduce processing costs and limit gear processing efficiency, and achieve stable and ideal processing quality. The effect of reducing tooth profile cutting process and improving production efficiency
- Summary
- Abstract
- Description
- Claims
- Application Information
AI Technical Summary
Problems solved by technology
Method used
Image
Examples
Embodiment Construction
[0024] The present invention is described in detail below with reference to accompanying drawing and embodiment:
[0025] attached Figure 1-3 It can be seen that a gear tooth bottom forming milling cutter includes a milling cutter body 1 and a cemented carbide blade, and the cutter body 1 is composed of several cemented carbide blades and fixing screws; the cutting position of the cutter body 1 is provided with a chip groove and cemented carbide blade assembly groove; cutter body 1 is provided with assembly shaft hole, radial positioning keyway, wheel hub 2 and fixed blade bolt hole; cemented carbide blade is fixed on the groove of cutter body by screws, and the blade is While finishing the bottom 12, the involute profile 13 of the tooth shape is rough cut; the top of the cutter body is provided with a top blade 10; the two sides of the cutter body are provided with side blades 6; The top blade 10 is provided with a straight cutting edge and an arc cutting edge; the arc cutt...
PUM
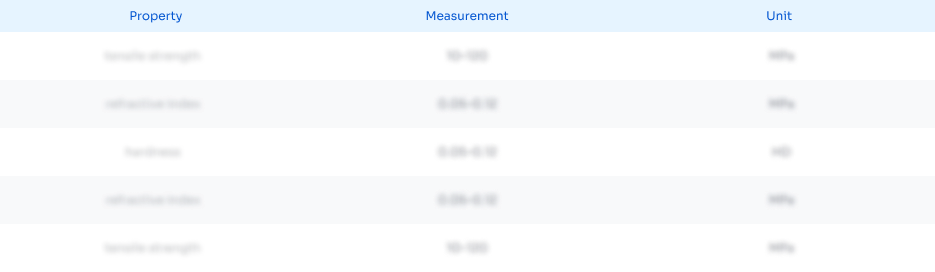
Abstract
Description
Claims
Application Information

- R&D
- Intellectual Property
- Life Sciences
- Materials
- Tech Scout
- Unparalleled Data Quality
- Higher Quality Content
- 60% Fewer Hallucinations
Browse by: Latest US Patents, China's latest patents, Technical Efficacy Thesaurus, Application Domain, Technology Topic, Popular Technical Reports.
© 2025 PatSnap. All rights reserved.Legal|Privacy policy|Modern Slavery Act Transparency Statement|Sitemap|About US| Contact US: help@patsnap.com