Production method for extracting lignite wax from brown coal
A technology for montan wax and lignite, which is applied in the field of chemical material preparation, can solve the problems of residual benzene solvent, high energy consumption, low production cost, etc., and achieves the effects of high solvent purity, good product quality, and reduced solvent amount
- Summary
- Abstract
- Description
- Claims
- Application Information
AI Technical Summary
Problems solved by technology
Method used
Image
Examples
Embodiment 1
[0038] (a) Multi-stage countercurrent pulse extraction: lignite particles are transported to the extractor by a material-sealed conveyor, and at 50°C, first soak and extract by spraying, soaking, and draining with an extraction solvent containing montan wax with a mass concentration of 4.0%, and then Respectively, the extraction solvents containing montan wax with a mass concentration of 3.5%, 2.5%, 1.5%, 0.5%, 0.2%, and 0.1% were successively sprayed, soaked, extracted, and drained in seven stages. In the extraction solvent, methanol and industrial n-hexane (content 60 %) is 0.5:1, the mass ratio of extraction solvent to lignite is 1.5:1, and the extraction cycle is repeated for 180 minutes, then sprayed and soaked with n-hexane solvent for extraction, and finally sprayed with methanol solvent for soaking and extraction to achieve multi-stage countercurrent pulse extraction;
[0039] (b) Negative pressure countercurrent film evaporation: the mixed solution containing montan w...
Embodiment 2
[0050] (a) Multi-stage countercurrent pulse extraction: lignite particles are transported to the extractor by a material-sealed conveyor, and at 55° C., first soak and extract by spraying and soaking an extraction solvent containing montan wax with a mass concentration of 3.8%, drain, and then Respectively through the extraction solvent containing montan wax with a mass concentration of 3.0%, 2.0%, 1.0%, 0.8%, 0.4%, and 0.05%, successively seven stages of spraying, immersion, extraction, and draining, the mass ratio of methanol and n-hexane in the extraction solvent is 0.8:1, the mass ratio of extraction solvent to lignite is 1.8:1, repeated cycle extraction for 120min, then spraying and soaking extraction with n-hexane solvent, and finally spraying and soaking extraction with methanol solvent to realize multi-stage countercurrent pulse extraction;
[0051] (b) Negative pressure countercurrent film evaporation: the mixed solution containing montan wax obtained by step (a) is fi...
PUM
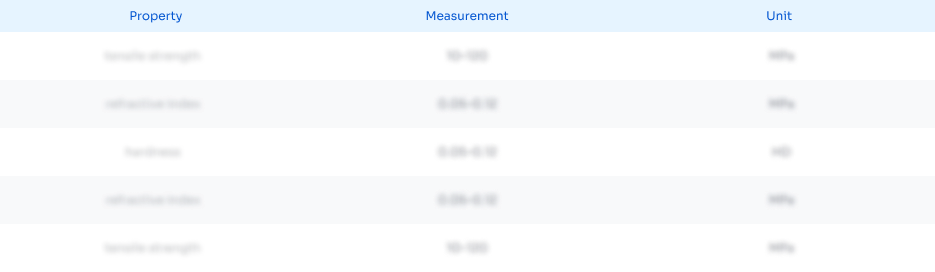
Abstract
Description
Claims
Application Information

- R&D
- Intellectual Property
- Life Sciences
- Materials
- Tech Scout
- Unparalleled Data Quality
- Higher Quality Content
- 60% Fewer Hallucinations
Browse by: Latest US Patents, China's latest patents, Technical Efficacy Thesaurus, Application Domain, Technology Topic, Popular Technical Reports.
© 2025 PatSnap. All rights reserved.Legal|Privacy policy|Modern Slavery Act Transparency Statement|Sitemap|About US| Contact US: help@patsnap.com