Acrylic ester electrostatic flocking binding agent and preparation method thereof
An electrostatic flocking and acrylate technology, applied in the direction of ester copolymer adhesives, adhesive types, non-polymer adhesive additives, etc., can solve the problems that cannot meet the requirements of electrostatic flocking fabrics at the same time, and achieve excellent anti-corrosion Stain resistance, excellent water resistance, excellent high temperature resistance effect
- Summary
- Abstract
- Description
- Claims
- Application Information
AI Technical Summary
Problems solved by technology
Method used
Image
Examples
Embodiment 1
[0031] Raw material ratio:
[0032] Lauryl alcohol polyoxyethylene (50) ether 1.2 grams, sodium lauryl sulfate 1.2 grams, itaconic acid 0.5 grams, N-methylol acrylamide 2.5 grams, acrylic acid 2 grams, butyl acrylate 75 grams, 21 grams of isooctyl acrylate, 10 grams of styrene, 2.39 grams of γ-methacryloxypropyl trimethoxysilane, 5 grams of epoxy resin E-44, 3.92 grams of adipate dihydrazide, 0.07 grams of sodium acetate gram, 0.4 gram of ammonium persulfate, 145 grams of deionized water;
[0033] Preparation:
[0034] 1) Take 50 grams of deionized water and all the emulsifiers, i.e. lauryl alcohol polyoxyethylene (50) ether, sodium lauryl sulfate, add them to the pre-milk kettle, fully dissolve, and then add the monomer i.e. itacan Acid, N-methylolacrylamide, acrylic acid, butyl acrylate, isooctyl acrylate, styrene and epoxy resin, fully stirred and emulsified to form a pre-emulsion;
[0035] 2) Mix 1% by weight of the pre-emulsion with γ-methacryloxypropyltrimethoxysilane...
Embodiment 2
[0042] Raw material ratio: 1.3 grams of lauryl alcohol polyoxyethylene (50) ether, 1.3 grams of sodium lauryl sulfate, 0.6 grams of itaconic acid, 2.6 grams of N-methylol acrylamide, 2.2 grams of acrylic acid, butyl acrylate 78 grams of ester, 23 grams of isooctyl acrylate, 11 grams of styrene, 2.54 grams of γ-methacryloxypropyl trimethoxysilane, 5.5 grams of epoxy resin E-44, 4.31 grams of adipate dihydrazide , 0.072 grams of sodium acetate, 0.43 grams of ammonium persulfate, 155 grams of deionized water, wherein the pre-milk still uses 60 grams of deionized water; the production process is the same as in Example 1.
Embodiment 3
[0044] Raw material ratio: 1.4 grams of lauryl alcohol polyoxyethylene (50) ether, 1.4 grams of sodium lauryl sulfate, 0.8 grams of itaconic acid, 2.8 grams of N-methylol acrylamide, 2.4 grams of acrylic acid, butyl acrylate 82 grams of ester, 25 grams of isooctyl acrylate, 11.5 grams of styrene, 2.7 grams of γ-methacryloxypropyl trimethoxysilane, 6 grams of epoxy resin E-44, 4.70 grams of adipate dihydrazide , 0.075 grams of sodium acetate, 0.45 grams of ammonium persulfate, 165 grams of deionized water, wherein the pre-milk kettle uses 70 grams of deionized water; the production process is the same as in Example 1.
PUM
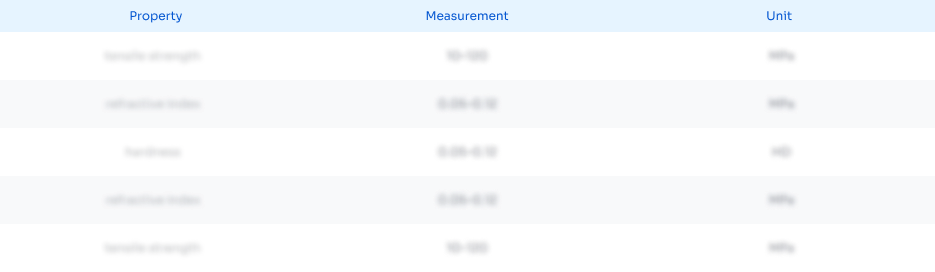
Abstract
Description
Claims
Application Information

- Generate Ideas
- Intellectual Property
- Life Sciences
- Materials
- Tech Scout
- Unparalleled Data Quality
- Higher Quality Content
- 60% Fewer Hallucinations
Browse by: Latest US Patents, China's latest patents, Technical Efficacy Thesaurus, Application Domain, Technology Topic, Popular Technical Reports.
© 2025 PatSnap. All rights reserved.Legal|Privacy policy|Modern Slavery Act Transparency Statement|Sitemap|About US| Contact US: help@patsnap.com