Electrolyte for driving electrolytic capacitors
A technology of electrolytic capacitors and electrolytes, applied in electrolytic capacitors, capacitors, circuits, etc., can solve the problems of deterioration and oxidative deterioration of peripheral components such as sealants
- Summary
- Abstract
- Description
- Claims
- Application Information
AI Technical Summary
Problems solved by technology
Method used
Image
Examples
Embodiment
[0057] Below, examples are given to further specifically illustrate the present invention, but the present invention is not limited by these examples, and those skilled in the art can make a large number of modifications within the technical idea of the present invention. In the following examples and comparative examples, the PVA-based resin produced in the following production example 1 using each saponification catalyst shown in the following Table 1 as a saponification catalyst was used. It should be noted that PVA-based resins having different degrees of polymerization can be changed by adjusting the ratio of vinyl acetate monomer to methanol as a solvent and the polymerization yield when solution-polymerizing vinyl acetate monomer in the above-mentioned production examples. In addition, when copolymerizing an unsaturated monomer that can be copolymerized with vinyl acetate monomer, the unsaturated monomer is also added at one time at the beginning of the polymerization ...
manufacture example 1
[0060] After replacing the reactor with agitator, reflux condenser, nitrogen inlet pipe, thermometer and pressure gauge with nitrogen, drop into 2800 parts by mass of deoxidized vinyl acetate monomer and 800 parts by mass of methanol after deoxidation, and stir After starting to raise the temperature at the bottom to reach 60°C, add 50 parts by mass of an initiator (2,2'-azobis(2,4-dimethylvaleronitrile)) dissolved in 50 parts by mass of methanol that has been deoxygenated separately. Initiator solution to initiate polymerization. After polymerizing at 60° C. for 5 hours, cooling was performed to stop the polymerization. The solid content concentration in the polymerization solution at this time was 55.1% (71.8% in terms of polymerization yield). In addition, the obtained polyvinyl acetate resin was made into polyvinyl alcohol with a degree of saponification of 100 mol% and was prepared according to JIS K- The degree of polymerization obtained by measuring in 6726 (1994) was ...
manufacture example 2~24
[0062] Change the feeding ratio of vinyl acetate monomer and methanol, the amount of initiator, and the polymerization yield to prepare polyvinyl acetate-methanol solutions with different degrees of polymerization, and change the saponification catalyst to the type shown in Table 1 to perform saponification. When the saponified gel cannot be pulverized or is in a liquid state, it is directly dried, and after drying, it is pulverized into about 3 mm to about 10 mm. Except for this, the same operation as that of Production Example 1 was performed, and PVA2-24 shown in Table 1 were produced, respectively.
[0063] [Table 1]
[0064]
[0065] The saponification catalysts in Table 1 are as follows.
[0066] 1) tert-butylimino-tris(pyrrolidinyl)phosphorane
[0067] 2) 2-tert-butylimino-2-diethylamino-1,3-dimethylperhydro-1,3,2-diacriphosphorin
[0068] 3) Tetramethylammonium hydroxide
[0069] 4) Benzyltrimethylammonium hydroxide
[0070] 5) 7-methyl-1,5,7-triazabicyclo[4.4....
PUM
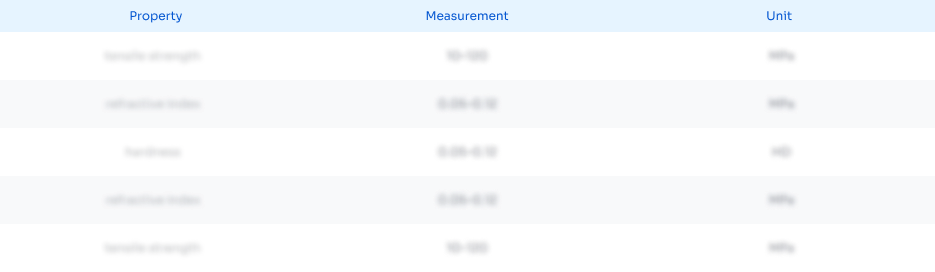
Abstract
Description
Claims
Application Information

- R&D Engineer
- R&D Manager
- IP Professional
- Industry Leading Data Capabilities
- Powerful AI technology
- Patent DNA Extraction
Browse by: Latest US Patents, China's latest patents, Technical Efficacy Thesaurus, Application Domain, Technology Topic, Popular Technical Reports.
© 2024 PatSnap. All rights reserved.Legal|Privacy policy|Modern Slavery Act Transparency Statement|Sitemap|About US| Contact US: help@patsnap.com