Preparation method of photocatalytic functional fabric based on titanium dioxide/magnesium oxide core-shell nanorod
A technology of functional fabrics and titanium dioxide is applied in the field of preparation of photocatalytic functional fabrics, which can solve problems such as no reports and achieve the effect of improving photocatalytic activity.
- Summary
- Abstract
- Description
- Claims
- Application Information
AI Technical Summary
Problems solved by technology
Method used
Image
Examples
Embodiment 1
[0022] Add 0.65g PVP to 5ml DMF solvent to form a solution with a mass volume ratio (g / ml) of 13:100, add 0.6ml Triton X-100 and 0.65g Mg(NO 3 ) 2 ·6H 2 O, magnetic stirring for 8h to obtain the precursor spinning solution 1 of MgO. Add 0.52g PVAc to 4ml DMF solvent to form a solution with a mass volume ratio (g / ml) of 13:100, add 0.6ml Triton X-100, 0.4ml HAc and 1.04g TTIP to the solution, and stir magnetically for 8h to obtain TiO 2 The precursor spinning solution 2; the MgO precursor spinning solution 1 and TiO 2Precursor spinning solution 2 is respectively packed in respective injector 3 and injector 4, and the high voltage source 7 of 18kV is added between coaxial spinneret 5 and receiving plate 6, and the distance from spinneret to receiving plate is 12cm, Under the action of the electric field, the charged droplets overcome their own surface tension to form a jet stream; the extrusion rates of the syringe 3 and the syringe 4 are controlled by the micro-injection pu...
Embodiment 2
[0024] Add 0.65g PVP to 5ml DMF solvent to form a solution with a mass volume ratio (g / ml) of 13:100, add 0.6ml Triton X-100 and 0.65g Mg(NO 3 ) 2 ·6H 2 O, magnetic stirring for 8h to obtain the precursor spinning solution 1 of MgO. Add 0.52g PVAc to 4ml DMF solvent to form a solution with a mass volume ratio (g / ml) of 13:100, add 0.6ml Triton X-100, 0.4ml HAc and 1.04g TTIP to the solution, and stir magnetically for 8h to obtain TiO 2 The precursor spinning solution 2; the MgO precursor spinning solution 1 and TiO 2 Precursor spinning solution 2 is packed into syringe 3 and syringe 4 respectively, and 18kV high voltage source 7 is added between coaxial spinneret 5 and receiving plate 6, and the distance from spinneret to receiving plate is 12cm, charged Under the action of an electric field, the droplets overcome their own surface tension to form a fine jet; the extrusion rates of the syringes 3 and 4 are controlled by two micro-injection pumps 8 and 9, respectively, that...
Embodiment 3
[0026] Add 0.65g PVP to 5ml DMF solvent to form a solution with a mass volume ratio (g / ml) of 13:100, add 0.6ml Triton X-100 and 0.65g Mg(NO 3 ) 2 ·6H 2 O, magnetic stirring for 8h to obtain the precursor spinning solution 1 of MgO. Add 0.52g PVAc to 4ml DMF solvent to form a solution with a mass volume ratio (g / ml) of 13:100, add 0.6ml Triton X-100, 0.4ml HAc and 1.04g TTIP to the solution, and stir magnetically for 8h to obtain TiO 2 The precursor spinning solution 2; the MgO precursor spinning solution 1 and TiO 2 Precursor spinning solution 2 is packed into syringe 3 and syringe 4 respectively, and 18kV high voltage source 7 is added between coaxial spinneret 5 and receiving plate 6, and the distance from spinneret to receiving plate is 12cm, charged The droplet overcomes its own surface tension under the action of an electric field to form a jet stream; the extrusion rates of the syringes 3 and 4 are controlled by two micro-injection pumps 8 and 9, respectively, that ...
PUM
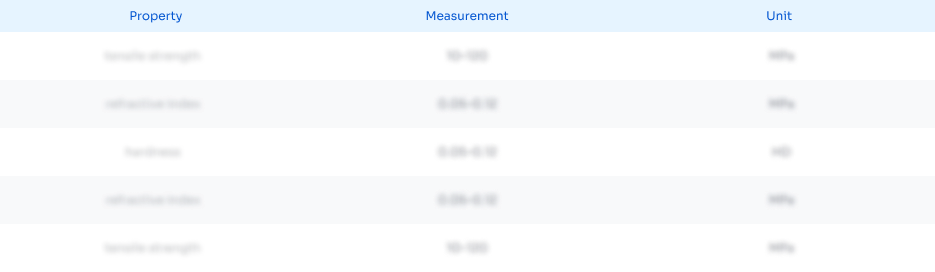
Abstract
Description
Claims
Application Information

- R&D Engineer
- R&D Manager
- IP Professional
- Industry Leading Data Capabilities
- Powerful AI technology
- Patent DNA Extraction
Browse by: Latest US Patents, China's latest patents, Technical Efficacy Thesaurus, Application Domain, Technology Topic, Popular Technical Reports.
© 2024 PatSnap. All rights reserved.Legal|Privacy policy|Modern Slavery Act Transparency Statement|Sitemap|About US| Contact US: help@patsnap.com