Method for controlling gas backflow in melting reduction smelting
A technology of coal gas and cold gas, which is applied in the field of gas reverse channeling control in smelting reduction smelting, which can solve the problems of lower qualified rate of molten iron, fluctuation of factory pressure, fluctuation of gasifier furnace condition, etc., to reduce the probability of shaft furnace agglomeration, Improvement of operating rate and output and reduction of wind down time
- Summary
- Abstract
- Description
- Claims
- Application Information
AI Technical Summary
Problems solved by technology
Method used
Image
Examples
Embodiment 1
[0026] By adopting the method of the present invention, the powder addition in the center of the shaft furnace (0% powder addition) is cancelled, the cold gas is introduced into the cold gas pipeline 4, the temperature of the downcomer is controlled between 650~750°C, the melting rate is 138t / h, and the shaft furnace pressure The difference is 47kPa, the metallization rate is 65%, the average downcomer blockage is 1.1 times / month, the fuel ratio is 991kg / thm, and the coke ratio is 153kg / thm.
Embodiment 2
[0028] By adopting the method of the present invention, the addition of powder in the center of the shaft furnace (0% powder addition) is cancelled, cold gas is passed into the cold gas pipeline 4, nitrogen gas is passed into the nitrogen gas pipeline 5, and the temperature of the downcomer is controlled between 650 to 750°C. The rate is 138t / h, the pressure difference of the shaft furnace is 45kPa, the metallization rate is 57%, the downcomer blockage is 0.9 times / month on average, the fuel ratio is 1010kg / thm, and the coke ratio is 186kg / thm.
PUM
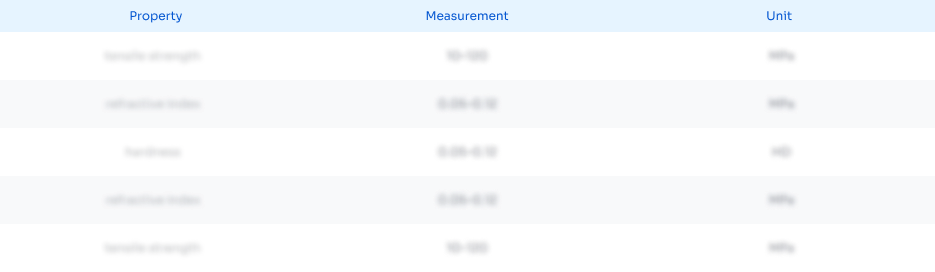
Abstract
Description
Claims
Application Information

- R&D
- Intellectual Property
- Life Sciences
- Materials
- Tech Scout
- Unparalleled Data Quality
- Higher Quality Content
- 60% Fewer Hallucinations
Browse by: Latest US Patents, China's latest patents, Technical Efficacy Thesaurus, Application Domain, Technology Topic, Popular Technical Reports.
© 2025 PatSnap. All rights reserved.Legal|Privacy policy|Modern Slavery Act Transparency Statement|Sitemap|About US| Contact US: help@patsnap.com